Ford reveals plans for massive EV and battery factories in the US
Ford and South Korean battery manufacturer SK Innovation will spend a combined $11.4 billion to build several new factories in the Tennessee and Kentucky focused on the development and production of electric vehicles and the batteries that power them.
The new facilities represent the first new plants built by Ford, completely from scratch, in over 50 years. The Tennessee plant will be a “mega campus” that houses a vehicle-production facility for Ford’s F-series pickup trucks and a battery assembly division, while the twin factories in Kentucky will manufacture lithium-ion batteries.
The facilities won’t come online until 2025, but Ford CEO Jim Farley says the investment signals the seriousness with which the company is taking its commitment to EVs. The new campus in Stanton, Tennessee, for example, will cover nine square miles and represents the largest facility ever built in the company’s 118-year history, Farley said.
“This is a new Ford,” Farley told The Verge. “This is show, not tell time.”
Ford, like the rest of the auto industry, is scrambling to shift its attention to EVs, even as they only represent a small fraction of vehicles sold every year. The announcement comes as Congress is debating whether to approve an infrastructure deal that would fund the construction of hundreds of thousands of new charging stations, as well as new consumer incentives for EV sales. It also comes as the auto industry grapples with new proposals banning the sale of gas cars in foreign markets and some US states like California.
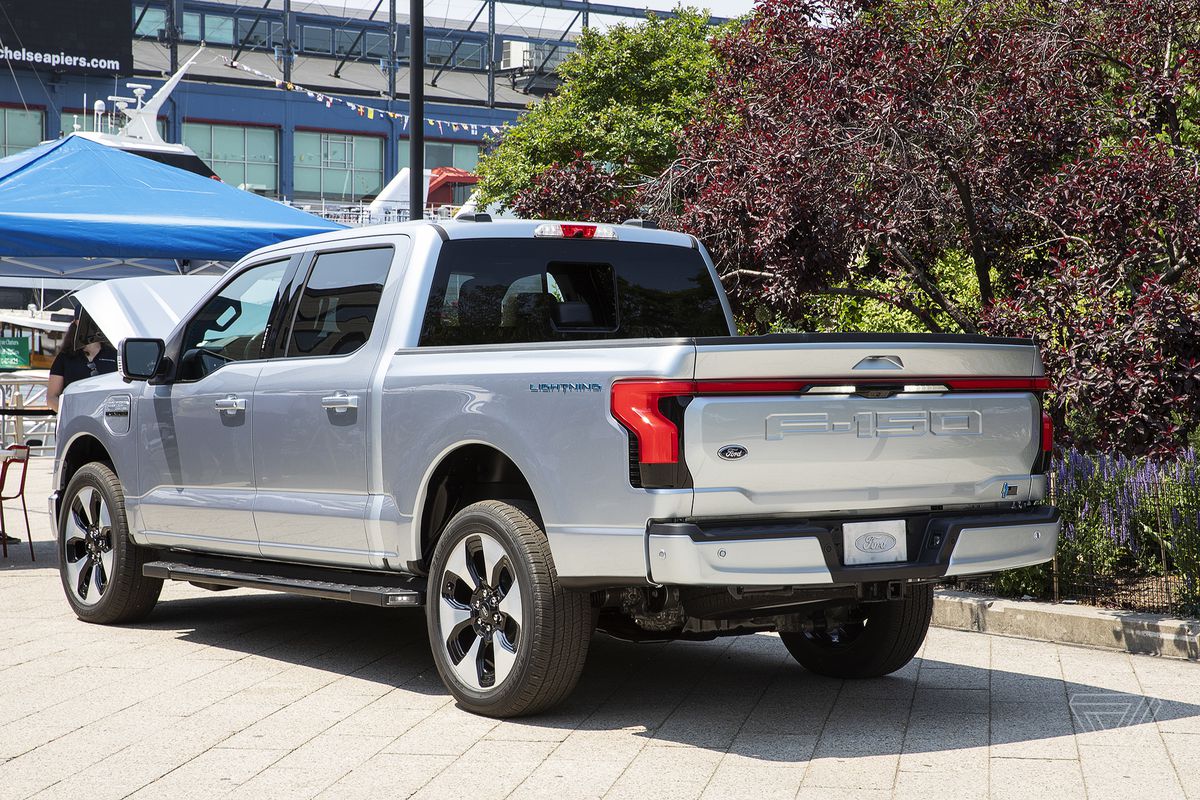
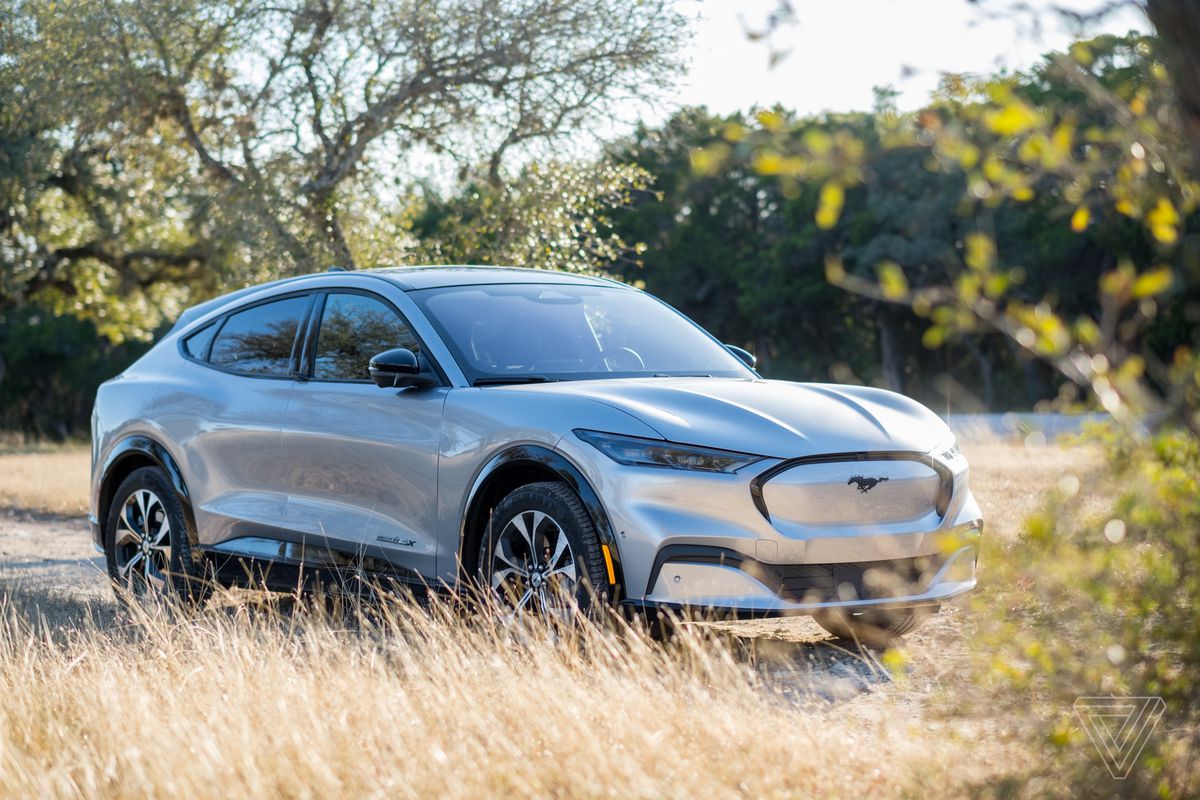
Farley made the analogy that electric cars are now at a similar place as smartphones in 2007. “This story … is not about propulsion,” Farley said. “This story is about digital vehicles with embedded systems, and a customer experience led through software that gets better every day, and changes the definition of a car from something that gets you from point A to point B, to something that enables your full life.”
The new facilities represent a shift in Ford’s approach to EV manufacturing. It’s a more financially risky move with potentially lucrative rewards in the future if the company can successfully supplement production from its own suppliers.
Ford currently sources its batteries from SK Innovation, which recently lost a trade secret dispute with rival LG Chem that could hinder its imports to the US. (The companies recently reached an agreement that could avert a possible import ban.) By making its own batteries in the US, Ford can avoid some of the conflicts that arise from sourcing batteries overseas.
Farley estimates that Ford will need 140GWh of battery manufacturing capacity a year, and in total, the company’s three new battery plants will enable 129 gigawatt-hours (GWh) a year of production capacity. By comparison, General Motors is planning four new battery factories in the US with partner LG Chem for a total annual capacity of 140GWh, while Volkswagen is aiming to have six battery cell production plants operating in Europe by 2030 for a total of 240GWh a year. And Tesla CEO Elon Musk has said his company’s first battery factory in Berlin would produce 250GWh — roughly equivalent to the current world battery cell production capacity.
Globally, battery production is expected to grow from 95.3GWh in 2020 to 410.5GWh in 2024, according to GlobalData, a data and analytics company.
Farley said Ford’s contribution to the massive investments in battery capacity will be significant because of its status as maker of the F-150 pickup truck, which has been the most popular vehicle in the US for decades. “This is different than Tesla and the other announcements [because] this is enormous scale,” he said. “America’s best selling vehicles going electric. We’re totally sold out.”
Ford says it will spend $7 billion, while SK Innovation will contribute $4.4 billion, for a total of $11.4 billion. Previously, Ford has said it would spend $30 billion by 2025, and that 40 percent of its global fleet will be electric by 2030. The company is currently at work retrofitting its historic Rouge factory for the production of the all-electric Ford F-150 Lightning pickup truck.
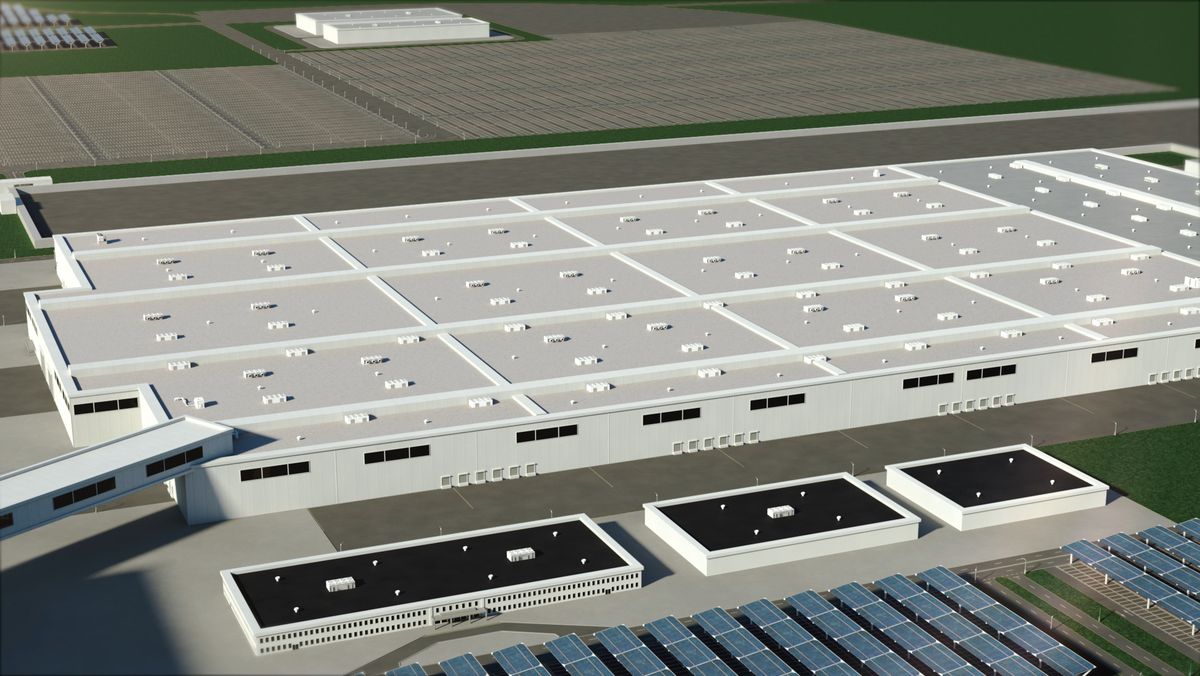
The “mega campus” in Stanton, Tennessee, will be called Blue Oval City. At a cost of $5.6 billion, the facility will generate approximately 6,000 new jobs, Ford says. Blue Oval City will become a “vertically integrated ecosystem” for Ford’s assembly of an expanded lineup of electric F-series vehicles. It will also include a battery plant, key suppliers, and recycling. (Ford recently struck a deal with Redwood Materials, a battery recycler founded by a former top executive from Tesla.) Ford said that Blue Oval City is also designed to be carbon neutral with “zero waste to landfill” once fully operational.
In central Kentucky, Ford plans to build a “dedicated battery manufacturing complex” with SK Innovation. Dubbed the BlueOvalSK Battery Park, the complex will cost $5.8 billion and create 5,000 jobs. Batteries for the company’s next-generation Ford and Lincoln EVs will be assembled at the site’s twin battery plants. The construction money will flow from a new joint venture called BlueOvalSK (which is still subject to “regulatory approvals and other conditions,” Ford says).
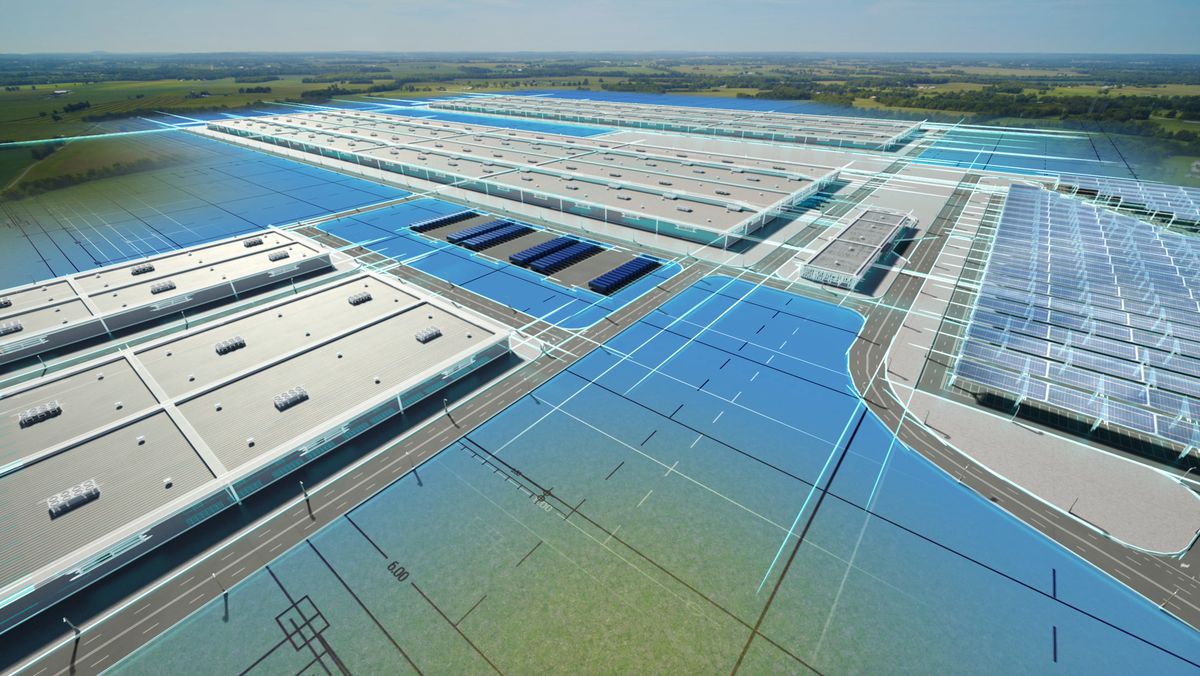
Ford projects that it will create a total of 11,000 new jobs in the two states. As such, the company says it is prepared to spend $525 million on a nationwide job training program, starting with $90 million on a pilot project in Texas. The hope is to train the next generation of workers on the intricacies of EV manufacturing and maintenance, not only to work at Ford’s factories but also at its dealerships and to make repairs in the field.
“Our industry has an enormous shortage of technicians,” Farley said. “We need to recruit a huge number of technicians who are good at doing service on the road.”
Ford is receiving financial incentives from both states in exchange for agreeing to build there. Tennessee and Kentucky are also both contributing money in the form of training grants to ensure that future workers have the necessary skills. But Farley said the primary consideration was finding locations with competitive energy rates, since a battery plant uses five times the energy of a traditional assembly plant. Ford also prioritized finding “greenfield” sites with no prior environmental issues so that it could build quickly. “We need to move fast,” said Farley.
Ford’s shift to electric vehicles has not been without its speed bumps. This week, the company issued two recalls for its Mustang Mach-E, after determining that the adhesive used to attach the windshield and optional glass roof wasn’t secure enough. It was the Mach-E’s second recall, after an earlier investigation discovering loose subframe bolts. Customer deliveries of the Mach-E were delayed, too, after the company discovered a software problem that led to the 12-volt battery dying, as The Verge first reported in April.
When asked about the recalls, Farley acknowledged that Ford has “a lot of work to do as a company around quality” and added “we have to get it right.” He also employed a baseball metaphor that he is fond of using in media interviews. “This is the first inning,” he said. “But boy, the demand is strong. And people absolutely love this car. We just have to make it better every day. And that’s on us.”
https://www.theverge.com/2021/9/27/22696427/ford-ev-battery-factory-tennessee-kentucky-investment