Solid-state polymer heat pump gets rid of the heat itself
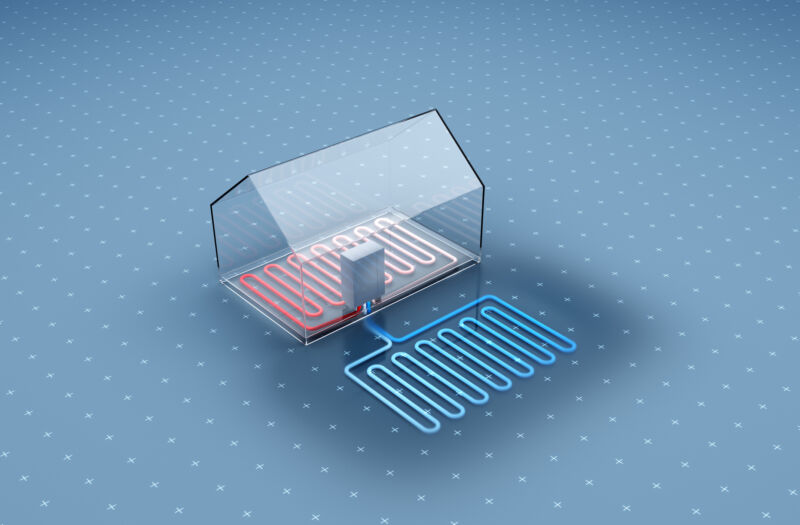
Heat pumps are the most energy-efficient way of controlling indoor temperature. By moving heat between locations, they avoid the inefficiencies of generating heat in the first place. But that doesn’t mean they can’t be made more efficient.
Most current heat pumps rely on materials that exhibit large changes in temperature in response to changing pressures, but the energy required to pressurize them gets lost when they’re cycled back to a low-pressure state, absorbing heat from their surroundings. That has gotten people interested in electrocaloric devices, where changes in temperature are driven by storing charges in a material. Since it essentially acts as a big capacitor, much of the electrical energy involved can be pulled back out as the system cycles.
But capacitors aren’t especially mobile, so electrocaloric systems tended to use fluids to move heat into and out of the capacitor as it cycles. Now, however, researchers have developed an electrocaloric system that moves itself between hot and cold environments, radically simplifying the system and eliminating some of the energy required for it to operate. They even demonstrate it effectively cooling a computer chip.
Electrocalorics and heat pumps
Late last year, we covered a paper that described a demonstration electrocaloric system. It operated pretty simply: Pumping electrons into a capacitor caused a phase transition in its internal electronic structure. While this phase transition doesn’t involve melting or freezing, it is associated with a major change in the capacitor’s heat content.
But, on its own, that won’t operate as a heat pump. While it will happily either heat or cool its immediate environment (depending on whether it’s being charged or discharged), that doesn’t help you transfer heat between environments. To heat or cool an environment, you need to move heat energy out of or into the capacitor. The team that developed this device did so by simply pumping water.
So, to act as a cooling device, the electrocaloric capacitor would first heat up water that would then be pumped to where it could radiate that heat away to the environment. New water would then be pumped in, which the capacitor would cool during discharge. That cool water would then be pumped to where it could absorb heat from the area that was meant to be cooled.
It definitely works, but there is an energy cost associated with doing that pumping. The new work, done by researchers at the Shanghai Jiao Tong University, gets rid of the need for any pumping. Instead, the capacitor itself moves between the heat source and heat sink. And it does so when powered by the same thing that triggers the temperature change: being charged or discharged.
The work relies on a polymer called poly(vinylidene fluoride-trifluoroethylene-chlorofluoroethylene), a name so complex that even the abbreviation is excessively long (we’ll just refer to “the polymer”). It’s a known electrocaloric material, but variants of the polymer with a different chemical bonding structure have a different response to picking up charges: They change shape.
So, the researchers spent a fair bit of time testing chemical reactions that produced polymers with different frequencies of double bonds, attempting to maximize both effects: electrocaloric temperature changes and charge-driven shape changes. This was undoubtedly a significant amount of work, but it takes up roughly three sentences in the paper. In any case, with the chemistry sorted out, they could make a single polymer that had strong temperature and shape responses.
https://arstechnica.com/?p=2023270