These are the types of inventory your business can have
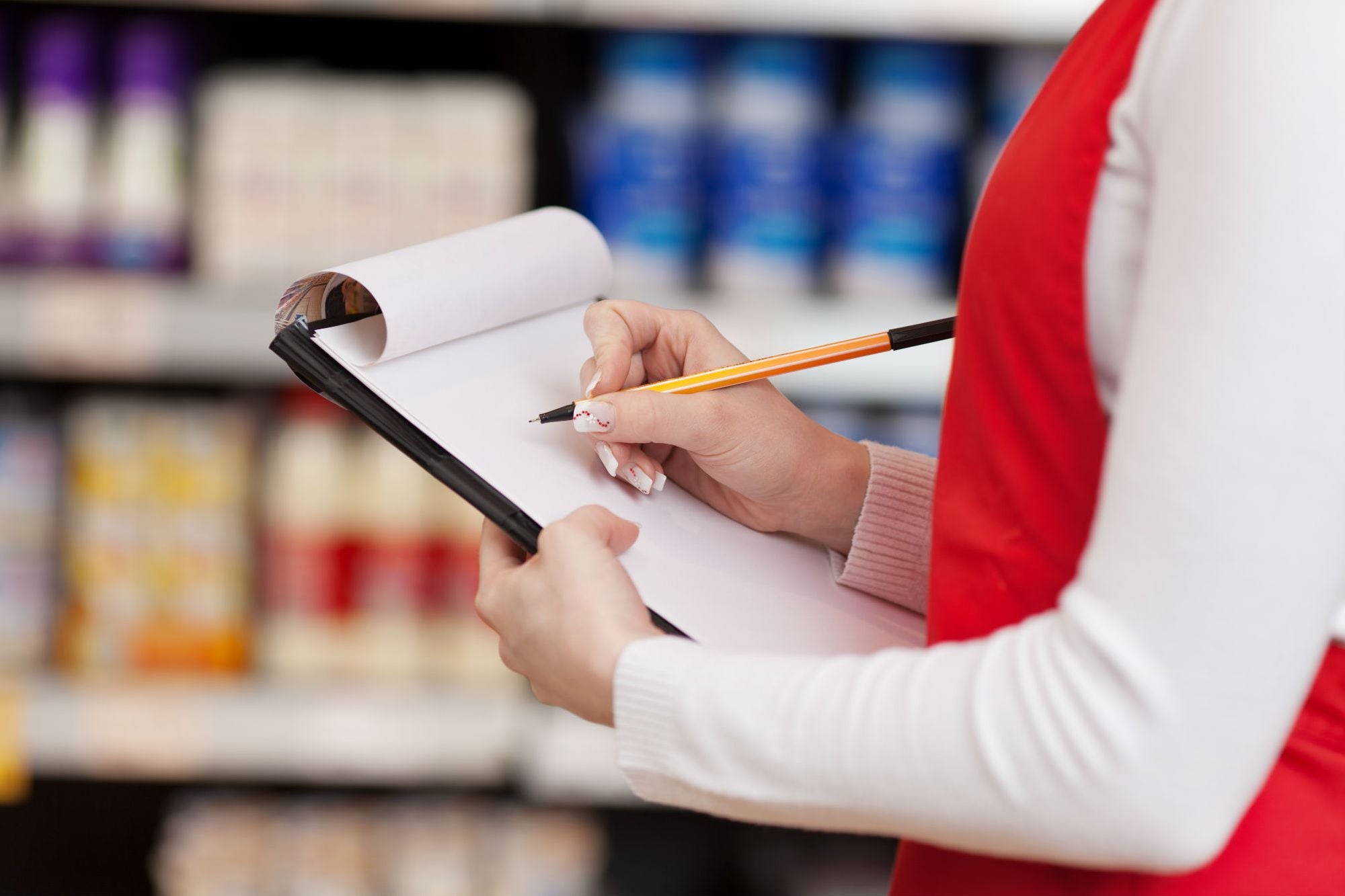
Every good entrepreneur knows that the basis of any commercial enterprise is the purchase and sale of goods and services. This is where the importance of inventory management comes from it. This accounting management will allow the company to maintain control in a timely manner, as well as to know at the end of the accounting period a reliable status of the economic situation of the company.
The main purpose of the inventory is to provide the company with the necessary materials, for its continuous and regular development, that is, the inventory has a vital role for consistent and coherent operation within the production process and thus meet the demand.
Some people who are primarily concerned with costs and finances will answer that inventory is money, an asset, or cash in the form of material. Inventories have a value, particularly in buying or selling businesses, and their value is always shown on the asset side of the Balance Sheet .
According to the functions and needs of a company there is a very wide variety of inventories, today we summarize them in 23 types:
1. Perpetual Inventory. It is the one that is kept in continuous agreement with the stocks in the warehouse, by means of a detailed record that can also serve as an auxiliary major, where the amounts in monetary units and the physical quantities are kept. At short intervals, inventory is taken from different sections of the warehouse and quantities or amounts or both are adjusted, when necessary, according to the physical account. Perpetual records are useful for preparing monthly, quarterly, or provisional financial statements. The perpetual system offers a high degree of control, because inventory records are always up to date.
2. Intermittent Inventory. It is an inventory that is carried out several times a year. It is resorted to, for various reasons, it cannot be entered in the accounting of the permanent stock inventory, to which it is a question of supplying in part.
3. Final Inventory. It is the one carried out by the merchant at the close of the financial year, generally at the end of a period, and serves to determine a new financial situation in that sense, after carrying out all the commercial operations of said period.
4. Initial Inventory. It corresponds to the one carried out at the beginning of operations.
5. Physical Inventory. It is the actual inventory. It is to count, weigh or measure and write down each and every one of the different classes of goods (merchandise) that are in stock on the inventory date, and evaluate each of these items. It is made as a detailed and valued list of stocks.
6. Inventory determined by observation and checked against a tally list. Inventory calculation made by listing the stock actually owned. The purpose of this inventory is to convince the auditors that the inventory records accurately represent the value of the main asset. The preparation for conducting the physical inventory consists of four phases: Inventory management (preparations), Identification, Instruction and Training.
7. Inventory in Transit. They are used in order to sustain operations to supply the conduits that link the company with its suppliers and its customers, respectively. They exist because the material must move from one place to another. While inventory is on the way, it cannot have a useful function for plants or customers, it exists exclusively for transportation time.
8. Inventory of Raw Material. They represent stocks of basic material inputs that are ready to be incorporated into a company’s manufacturing process.
9. Inventory in Process. They are inventories that are kept as labor, other materials and other indirect costs are added to the gross raw material, which will become either a sub-assembly or component of a finished product; As long as its manufacturing process is not completed, it must be inventory in process.
10. Inventory on Consignment. It is that merchandise that is delivered to be sold but the property title is kept by the seller.
11. Minimum Inventory. It is the minimum amount of inventory to be kept in the warehouse.
12. Available Inventory . It is one that is available for production or sale.
13. Inventory Online. It is that inventory that awaits to be processed in the production line.
14. Added Inventory. It is applied when managing the stock of a single item represents a high cost, to minimize the cost impact on inventory management, items are grouped into families or another type of material classification according to their economic importance, etc.
15. Forecast Inventory. They are had in order to cover a perfectly defined future need. It differs from security, in that forecasting is taken in light of a need that is known with reasonable certainty and therefore involves less risk.
16. Inventory of Goods. It is made up of all those goods that belong to the company, whether commercial or commercial, which are bought and then sold without being modified. All merchandise available for Sale will be displayed in this Account.
17. Fluctuation Inventory. These are carried because the quantity and pace of sales and production cannot be decided exactly. These fluctuations in demand and supply can be offset by reserve or safety stocks. These inventories exist in work centers when the work flow cannot be fully balanced. These inventories can be included in a production plan so that production levels do not have to change to cope with random variations in demand.
18. Anticipation Inventory. They are those that are established in advance of periods of greatest demand, commercial promotion programs or even a plant closure period. Basically, lead-time inventories store labor-hours and machine-hours for future needs and limit changes in production rates.
19. Lot or lot size inventory . These are inventories that are ordered in lot size because it is cheaper to do so than to order when it is necessary to meet demand. For example, it may be more economical to carry a certain amount of inventory than to order or produce in large batches to reduce setup or order costs or to obtain discounts on purchased items.
20. Seasonal Inventories. Inventories used for this purpose are designed to more economically meet seasonal demand by varying production levels to meet fluctuations in demand. These inventories are used to smooth the production level of operations so that workers do not have to be hired or fired frequently.
21. Intermittent Inventory. It is an inventory carried out with a certain time and not once at the end of the accounting period.
22. Permanent Inventory. Method followed in the operation of some accounts, generally representative of stocks, whose balance must coincide at any time with the value of the stocks.
23. Cyclical Inventory. They are inventories that are required to support the decision to operate according to lot sizes. This occurs when instead of buying, producing or transporting inventories one unit at a time, it is possible to decide to work in batches, in this way, inventories tend to accumulate in different places within the system.
https://www.entrepreneur.com/article/369786