These self-morphing 3D wood shapes could be future of wood manufacturing
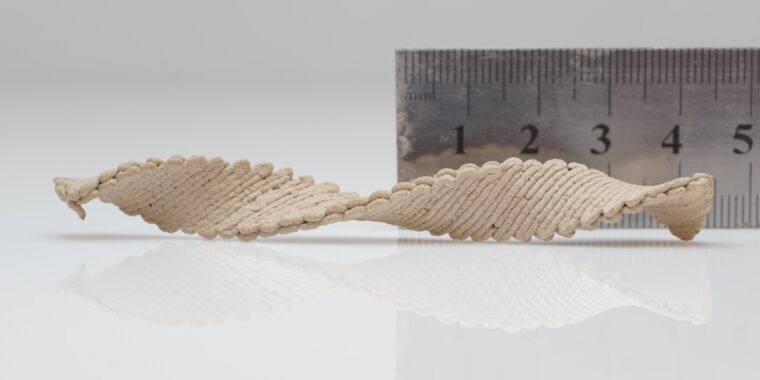
Scientists from The Hebrew University of Jerusalem have created wood ink that can be extruded into flat wooden structures, self-morphing into complex 3D shapes as they dry and shrink. The researchers presented their research at last week’s meeting of the American Chemical Society in Chicago. The technique could one day be used to make furniture or other wooden products that could be shipped flat to a destination and then dried to form the desired final shape.
As we’ve reported previously, developing novel shapeshifting materials is a very active area of research because there are so many promising applications, such as building artificial muscles—man-made materials, actuators, or similar devices that mimic the contraction, expansion, and rotation (torque) characteristics of the movement of natural muscle. The shape change comes about in response to an outside stimulus.
For instance, most artificial muscles are designed to respond to electric fields (such as electroactive polymers), changes in temperature (such as shape-memory alloys and fishing line), and changes in air pressure via pneumatics. In 2019, a team of Japanese researchers spiked a crystalline organic material with a polymer to make it more flexible, demonstrating their proof of concept by using their material to make an aluminum foil paper doll do sit-ups.
In 2020, MIT scientists successfully created flat structures that can transform into much more complicated structures, including a human face. These structures employed the same manufacturing technique as 3D printing but were designed to deform over time in response to changes in humidity and temperature. They might one day be used to make tents that can unfold and inflate on their own when temperature or other ambient conditions are changed. Other potential uses include deformable telescope lenses, stents, scaffolding for artificial tissue, and soft robotics.
Last year, Luxo, Jr., Pixar’s trademark animated Luxo balanced-arm lamp, helped inspire a novel approach to building multifunctional shapeshifting materials for robotics, biotechnology, and architectural applications. Physicists at Case Western Reserve University and Tufts University figured out how to remotely manipulate the ordinarily flat surface of a liquid crystal without any kind of external stimulus (such as pressure or heat), changing its physical appearance merely with the nearby presence of a bumpy surface. And scientists at Carnegie Mellon University created a simple mechanism to make flat pasta for shipping that takes on a specific 3D shape when cooked.
Typical manufacturing techniques treat materials like wood as passive objects to be actively shaped. “You press it, you bend it, you carve it, you machine it, in order to get the desired shape,” said Eran Sharon during a press conference at the ACS meeting. “If you look at nature, nothing is made this way. Tissue expands gently, and the shape emerges out of this distribution of different expansions and shrinkages. This is self-morphing. We wanted to go back to the origin of this concept, to nature, and do it with wood.”
https://arstechnica.com/?p=1876703