This EV truckmaker is gigacasting its battery packs for longevity
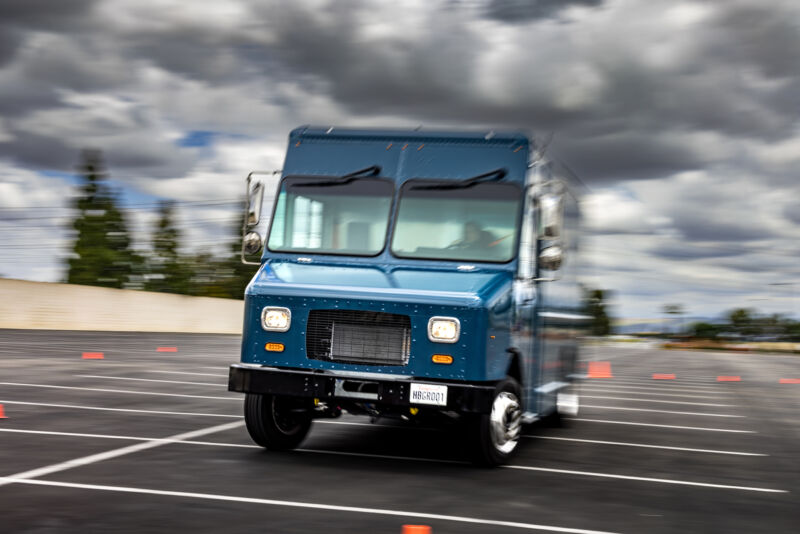
We make no secret of our affection for the electric vehicle here at Ars, and that extends beyond the light-duty cars and trucks we usually drive and write about. The commercial vehicle sector is electrifying, too, but most of what we’ve seen in terms of commercial EVs have been either at the lightest end of the scale—class 2 trucks like the Ford E-Transit and BrightDrop Zevo 600—or the biggest class 8 trucks like we’ve seen from Daimler, Volvo, and Tesla.
But what about a middle ground? One of the first companies to address the missing commercial EVs between the two ends of the spectrum is Harbinger, which has developed its own platform for class 4-7 EVs. It recently debuted a new medium-duty electric truck platform designed for last-mile delivery. Harbinger designed the powertrain in-house with durability in mind.
“When we look at the biggest product in our segment—for delivery vehicles anyways—it’s the Ford F-59, which is a stripped chassis, and that’s basically an engine with like minimal additional stuff,” Harbinger CEO John Harris told Ars. “It’s the same engine that Ford will put into an F-250. The engine has the durability, it can be mounted and handled properly, and there’s not much else there. But if we look at an EV, it’s much different. Its battery packs more than the drivetrain. And Ford doesn’t have a medium-duty toolbox for electrification.”
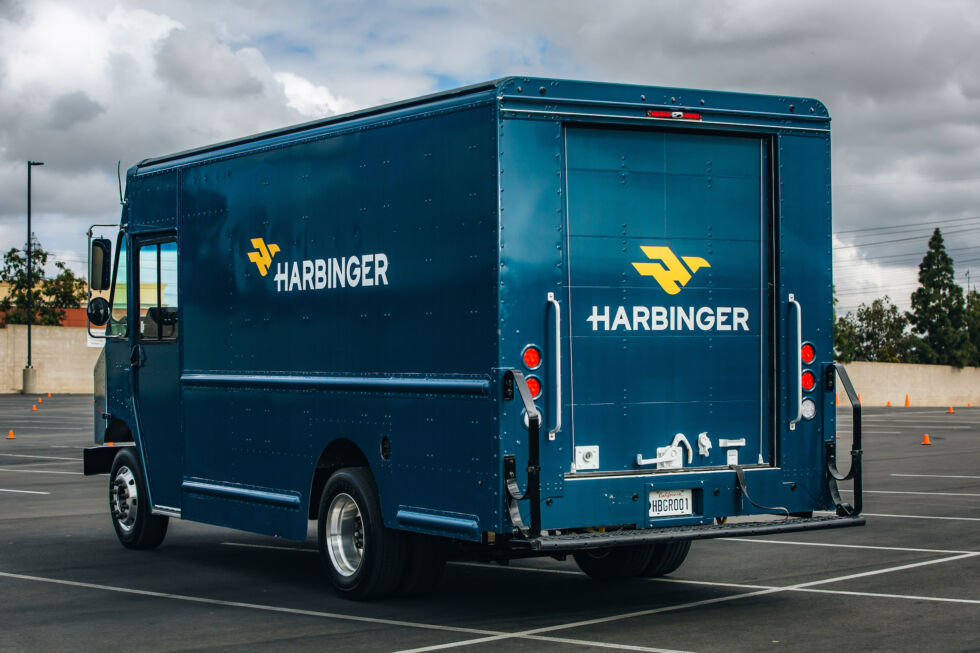
One problem is a customer base that expects to get plenty of use out of its trucks. “When you look at what we’re building, no one is OK with the class 4-6 truck unless it has 15 to 20 years of life,” Harris said. “At UPS, all the vehicles are on the road for 20 years. It’s not unusual for them to get to 25. And sometimes they replace engines in those vehicles in 15 years, but everything else is still good, so it’s worth doing. So here, when we look at every piece of the technology, we’re taking a different approach to get to that durability.” Consequently, Harbinger’s platform is designed for a 20-year, 450,000-mile (724,203-km) life.
For example: the battery pack. In a passenger car EV, the battery pack is usually built from stamped steel components, sealed together with body sealer. It’s great for mass production, according to Harris, “but when you look at a Tesla battery pack that’s 15 years old, and there’s a couple now, the cells are fine, the enclosures all rusted through.”
Harbinger has gone for a modular design that uses 2170 cylindrical cells, packed in increments of 35 kWh, each adding about 40 miles (64 km) of range. Instead of stamping the pack casing out of steel, it’s using a giant casting press to make a single-piece aluminum enclosure. “No welds, no sealer, no multi material joint. Tesla famously uses gigacasting to replace other stamp steel components in the body in white, but we’re applying that technology to battery packs instead,” Harris said.
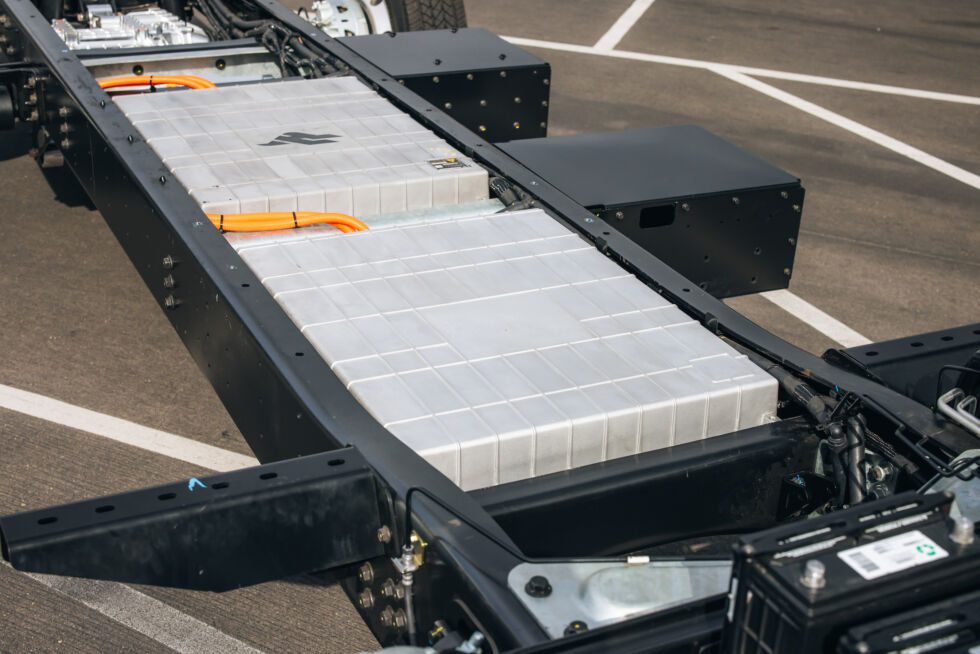
Like Porsche and Hyundai, Harbinger has opted for 800 V for its battery packs. The benefit here isn’t really for faster fast-charging; fleets of delivery trucks that rarely drive as much as 100 miles (160 km) a day will recharge slowly—but more importantly, much more cheaply—overnight. (The platform does have a capability for fast charging in up to an hour, however.)
“It’s positive mass and then efficiency by extension,” Harris said. The higher voltage means a lower current, which in turn means less weight; Harris said they can use a quarter of the amount of copper a 400 V architecture would require. “The other piece that makes a big difference is in drivetrains because when you look at the torque that you can get out of an electric motor, in many cases, it’s proportional to the voltage. So if you want a 400-volt motor, it’s way bigger.”
Harbinger is building its electric motors in-house, too, integrated into an eAxle drive unit that also combines a gearbox and inverter. Like the battery packs, it’s compact enough to fit between the chassis frame rails, which keeps the center of gravity low.
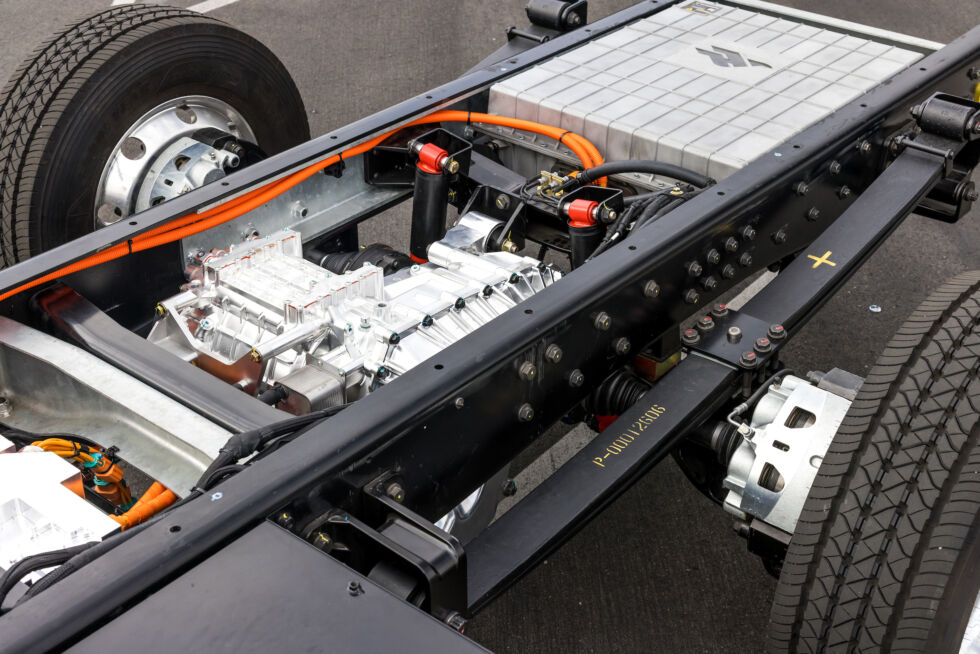
Because the design is meant to have some longevity in service, Harbinger has future-proofed with steer- and brake-by-wire so that an autonomous driving system could be integrated later. It could have already partnered with an AV developer to that end, but Harris thinks the decision of which AV developer to use will rest with individual fleet operators like UPS or, more specifically, their legal departments. “And then we need to just support that decision. And so we have, we think, the perfect platform for them. To then install their software, install their sensors, without having to break what we’ve already built,” Harris said.
Harbinger will deliver trucks to customer pilot programs later this year to begin validation. And the in-house design and manufacturing mean Harbinger’s trucks will cost about the same as an equivalent diesel or gasoline class 4 truck. Factor in reduced maintenance and much cheaper charging costs versus fuel bills, and it all seems rather encouraging.
https://arstechnica.com/?p=1951770