This is the world’s smallest 3D-printed wineglass, Swedish scientists claim
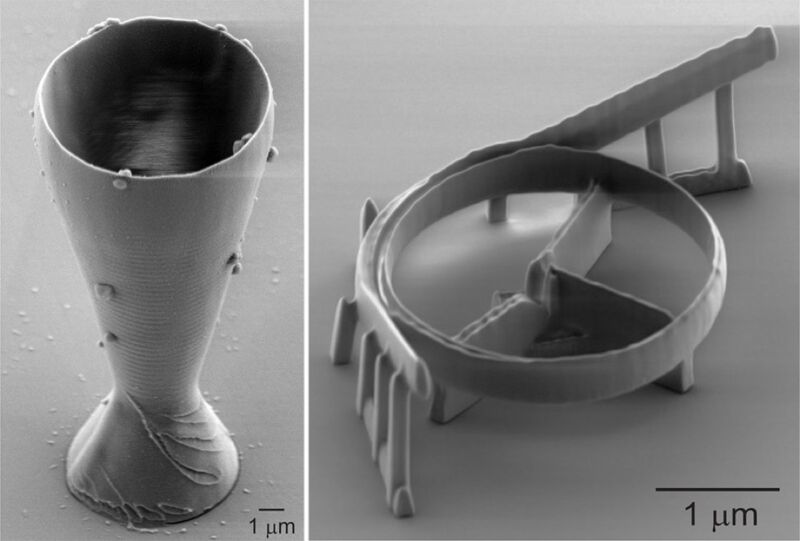
A team of Swedish scientists has developed a novel 3D-printing technique for silica glass that streamlines a complicated energy-intensive process. As a proof of concept, they 3D-printed the world’s smallest wineglass (made of actual glass) with a rim smaller than the width of one human hair, as well as an optical resonator for fiber optic telecommunications systems—one of several potential applications for 3D-printed silica glass components. They described their new method in a recent paper in the journal Nature Communications.
“The backbone of the Internet is based on optical fibers made of glass,” said co-author Kristinn Gylfason of the KTH Royal Institute of Technology in Stockholm. “In those systems, all kinds of filters and couplers are needed that can now be 3D printed by our technique. This opens many new possibilities.”
Silica glass (i.e., amorphous silicon dioxide) is one material that remains challenging for 3D printing, particularly at the microscale, according to the authors, though several methods seek to address that challenge, including stereolithography, direct ink writing, and digital light processing. Even those have only been able to achieve feature sizes on the order of several tens of micrometers, apart from one 2021 study that reported nanoscale resolution.
But all of those use sol-gel processes involving different organic mixtures loaded with silica nanoparticles. So the final printed structures are composites with many organic materials, hence lacking the most desired properties of silica glass (i.e., thermal and chemical stability, hardness, optical transparency over a broad range of wavelengths). It requires an extra sintering step at high temperatures of around 1,200° Celsius (2,192° F) for several hours to remove the organic residues and achieve those properties. That energy-intensive extra step severely limits potential applications since only substrate materials that can withstand such high temperatures can be used. Some approaches also require assembling 3D-printed structures into a final form, which is challenging at the micrometer scale.
When developing their alternative technique for 3D-printing silica glass, Gylfason et al. turned to hydrogen silsesquioxane (HSQ), an inorganic material that is similar to silica and can be patterned by electron beams, ion beams, and certain wavelengths of UV light. One major advantage is that their method does not rely on organic compounds to serve as photoinitiators or binders that stay on the substrate, as with stereolithography or direct ink writing. Instead, their method relies on direct cross-linking of the inorganic HSQ.
The process has three main steps. First, they drop-cast HSQ dissolved in organic solvents on a substrate. Once the HSQ dries, they trace the desired 3D shape using a focused sub-picosecond laser beam. Finally, any unexposed HSQ is dissolved with the handy application of a potassium hydroxide solution. Raman spectroscopy of the printed microstructures showed all the expected features for silica glass.
However, there were also traces of residual hydrogen and carbon. For applications requiring a more pure silica glass, the residual organics can be removed by annealing the structures at 900° Celsius (1,652° F)—an extra step, granted, but at a much lower temperature than the usual extra sintering step. After that, the spectrum for the structures matched that of a commercial fused silica glass substrate. While annealing 3D-printed microstructures can cause them to shrink or distort, the authors found that the maximum shrinkage for their silica glass structures was around 6 percent, compared to between 16 percent and 56 percent for glass objects made using stereolithography and direct ink writing methods.
In addition to the proof-of-concept tiny wine glass and optical resonator, the authors printed a tiny version of the KTH logo, a cantilever, and a conical spiral, as well as a silica glass optical fiber tip. They believe that their method could be used to make customized lenses for medical devices and micro-robots as well. Coating the 3D-printed microstructures with nanodiamonds or ferrous nanoparticles could enable further tailoring of properties for hybrid quantum photonics integration or magnetically remove motion control of the structures, respectively.
“The concerns when integrating 3D printing methods are usually different for different applications,” said co-author Po-Han Huang, a graduate student at KTH. “Even though optimization of our method is still required for different applications, we believe our method presents an important and necessary breakthrough for 3D glass printing to be used in practical scenarios.”
DOI: Nature Communications, 2023. 10.1038/s41467-023-38996-3 (About DOIs).
https://arstechnica.com/?p=1952140