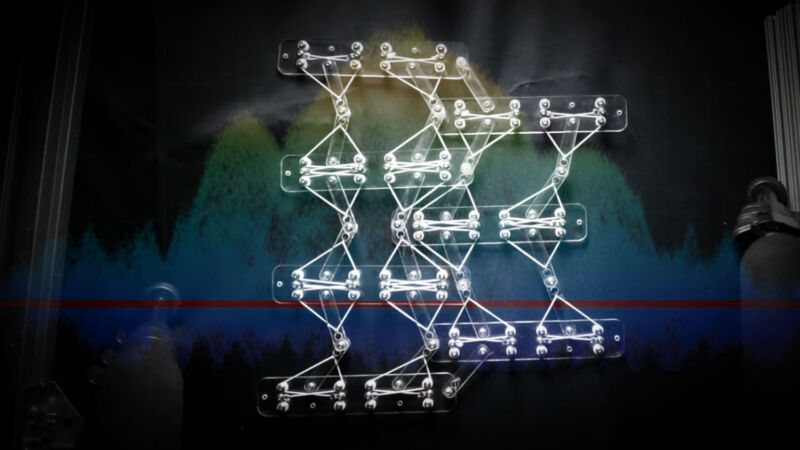
Luxo, Jr., Pixar’s trademark animated Luxo balanced-arm lamp, is based on a classic design known as the anglepoise lamp, invented by British designer George Carwardine in 1932. Almost ninety years later, the anglepoise lamp has helped inspire a novel approach to building multifunctional shapeshifting materials for robotics, biotechnology, and architectural applications, according to a new paper published in the Proceedings of the National Academy of Sciences.
Meanwhile, physicists at Case Western Reserve University and Tufts University have stumbled on another promising approach to creating novel shapeshifting materials. The researchers remotely manipulated the ordinarily flat surface of a liquid crystal without any kind of external stimulus (such as pressure or heat), changing its physical appearance merely with the nearby presence of a bumpy surface. It’s early days, but the researchers suggest their approach could someday enable materials that can shapeshift with the ease of The X-Men‘s Mystique. They described their work in a new paper published in the journal Physical Review Letters.
Developing novel shapeshifting materials is a very active area of research because there are so many promising applications, such as building artificial muscles—manmade materials, actuators, or similar devices that mimic the contraction, expansion, and rotation (torque) characteristics of the movement of natural muscle. For instance, in 2019, a team of Japanese researchers spiked a crystalline organic material with a polymer to make it more flexible, demonstrating their proof of concept by using their material to make an aluminum foil paper doll do sit-ups. Most artificial muscles are designed to respond to electric fields (such as electroactive polymers), changes in temperature (such as shape-memory alloys and fishing line), and changes in air pressure via pneumatics.
Later that same year, MIT scientists created a class of so-called “4D materials” that employ the same manufacturing technique as 3D printing but which are designed to deform over time in response to changes in the environment, like humidity and temperature. They’re also sometimes known as active origami or shape-morphing systems.
The MIT structures can transform into much more complicated structures than had previously been achieved, including a human face. These kinds of shapeshifting materials might one day be used to make tents that can unfold and inflate on their own, just by changing the temperature (or other ambient conditions). Other potential uses include deformable telescope lenses, stents, scaffolding for artificial tissue, and soft robotics.
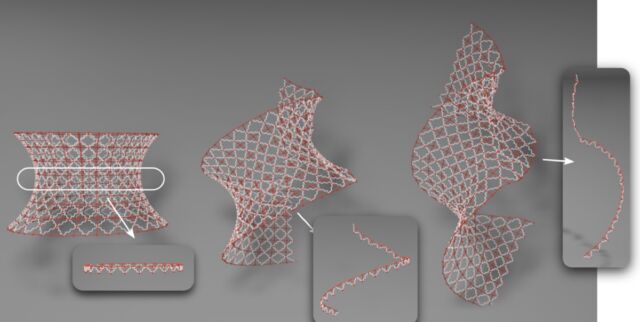
T is for Totimorphic
What’s unique about the latest research from the Harvard team is that their assemblies of interlocking blocks, or cells, can take on and maintain any number of configurations; most shapeshifting materials are limited to just a handful. That’s why they are called “totimorphic” structural materials.
“Today’s shapeshifting materials and structures can only transition between a few stable configurations, but we have shown how to create structural materials that have an arbitrary range of shape-morphing capabilities,” said co-author L Mahadevan of Harvard’s John A. Paulson School of Engineering and Applied Sciences (SEAS). “These structures allow for independent control of the geometry and mechanics, laying the foundation for engineering functional shapes using a new type of morphable unit cell.”
The trick to any shapeshifting material is to find the sweet spot where both rigidity and elasticity (or conformability) are optimized. If a material has too much conformability, it can’t maintain the different shapes it adopts because the configuration won’t be stable. If a material is too rigid, it won’t be able to take on new configurations at all. That’s where the anglepoise lamp comes in. The lamp head “is infinitely morphable by virtue of its having a set of opposing springs in tension that change their lengths while the total energy remains constant,” the authors wrote.
In other words, Luxo Jr.’s head will remain stable in any position because its springs will stretch and compress however they need to in order to counteract the force of gravity. The technical term is a “neutrally stable structure”: a structure in which the rigid and elastic elements are ideally balanced, enabling them to transition between an infinite number of positions or orientations while still remaining stable in all of them. Mahadevan and his colleagues essentially built an assembly using individual switchable hinges as building blocks to get the same balance between rigidity and conformability.
“By having a neutrally stable unit cell, we can separate the geometry of the material from its mechanical response at both the individual and collective level,” said co-author Gaurav Chaudhary, a postdoctoral fellow at SEAS. “The geometry of the unit cell can be varied by changing both its overall size as well as the length of the single movable strut, while its elastic response can be changed by varying either the stiffness of the springs within the structure or the length of the struts and links.”
As a proof of concept, the team demonstrated that a single sheet of their totimorphic cells could curve up, twist into a helix, bear weight, and even morph into face-like shapes. “We show that we can assemble these elements into structures that can take on any shape with heterogeneous mechanical responses,” said co-author S. Ganga Prasath, another SEAS postdoctoral fellow. “Since these materials are grounded in geometry, they could be scaled down to be used as sensors in robotics or biotechnology or could be scaled up to be used at the architectural scale.
https://arstechnica.com/?p=1806822