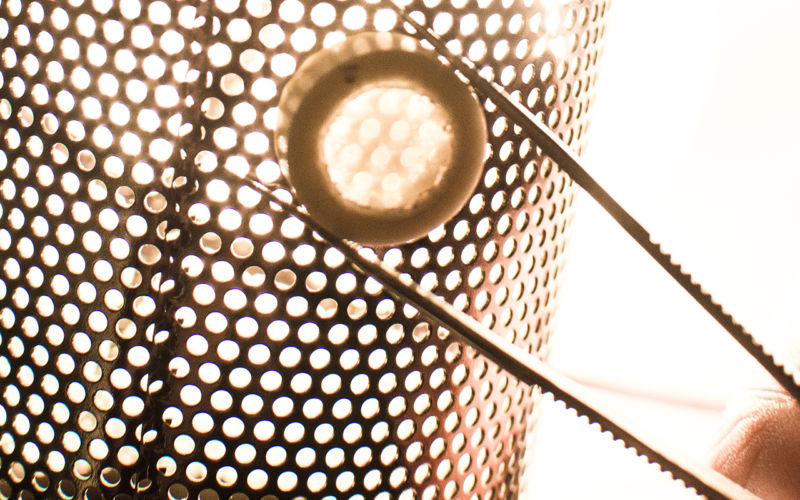
What makes a good construction material? There are many requirements, but one is the ability to efficiently connect different parts. Steel is almost the perfect example: you can join steel with fasteners (like nuts and bolts), by brazing, or by welding. The last of these is especially important. If we couldn’t weld metals, life would be quite different.
You don’t see this with ceramics. Ceramic parts are the hard-wearing miracle of modern life, but unlike steel and aluminum, you won’t find ceramics everywhere. This is because ceramics, though very useful, are difficult to work with. Joining two ceramics, or even connecting a ceramic to a metal, is a difficult and energy-consuming process because ceramics cannot be welded. That has changed, thanks to a team of researchers that is developing a ceramic welding laser.
Welding is riveting
Welding is a really special process. At one level, it is very simple: heat two materials until they melt and flow together. However, the melting is only local, so there is only minimal deformation to the rest of the part. The joint needs to be strong, which means that changes to the structure of the metal should not be too dramatic. Melting metals tend to oxidize vigorously, complicating the process.
Ceramic welding should be similar. The ceramic parts would be heated locally so that they melt and pool together. On cooling, the liquid recrystallizes to recreate the ceramic. Since ceramics are oxidized already, you don’t even have to worry too much about setting yourself on fire—a relief to me, as I have a bit of a flaming track record.
The problem is delivering heat to the right location. Since ceramics don’t conduct much heat, lasers are the weapon of choice for precision heating. Unfortunately, ceramics don’t efficiently absorb light; instead, they’re actually really good at scattering light. That means that the laser does not form a nice focus at the weld location and ends up gently heating a wide area of ceramic.
To weld, you have to focus
This is where the latest research comes in. First, scientists noted that there are a lot of applications for transparent ceramics. For these materials, laser light is not scattered and can form a good focus. The problem then becomes one of absorbing energy: a transparent material, by definition, does not absorb laser light, so it won’t heat up.
To understand how the researchers overcame this problem, we need to understand what makes a material transparent. To absorb light, an electron has to absorb a photon to move from one state to a higher energy state. Transparent (or white) ceramics have a crystal structure that puts a large gap between the low and high energy states. Most photons can’t push the electrons into the high-energy state and, so, pass through the material.
This means that to efficiently deliver energy to the weld, the laser wavelength would need to be in the ultraviolet—difficult but not impossible. The alternative is to use very short pulses of light with a longer wavelength. At the focus point of the laser, there are so many photons that an electron might absorb two photons simultaneously, gaining the required energy to move to a higher energy state. The advantage of this approach is that very high intensity is required to have enough photons, so the laser light is only absorbed when it is focused. This provides a high degree of control over where any melting happens.
The researchers demonstrated this using a laser that emitted light pulses that were between 0.2 and 2 picoseconds long (a picosecond is 10-12 seconds). They focused the light through a transparent ceramic cap so that it melted the ceramic just at the boundary between the cap and an underlying ceramic cylinder. After some tuning to determine how many pulses and what power were required to obtain the right amount of molten material (called the “melt pool”), they came up with a very good weld.
The data they present shows that their weld is sufficient to meet various packaging specifications required for electronics used in biomedical and space industries. Even better, because the photons are only absorbed at the focus, heat is delivered locally. Away from the weld, the ceramic remains nice and cool. The researchers showed that electronics could be packaged in transparent ceramics without damage.
It also turned out that slightly longer pulses (2 picoseconds) were better than short pulses. Short pulses either evaporated the material or did not have enough energy to melt the ceramic—the operating window for welding was very narrow.
Shooting light down the gap
For ceramics that are not transparent, scattering prevents the laser from focusing. However, the researchers found that if the edges of the ceramic are separated by just about the width of the focused laser beam, then enough energy is focused at the joint and at the right depth to melt material and form a weld. Again, the researchers demonstrated that nicely. In this case, the laser has to access the joint through that gap, so the joint cannot be buried. However, this is also the case for most metal welding techniques.
The laser that the researchers used was not particularly special, either. Lasers that generate picosecond pulses with average powers of 50W are not that hard to obtain. That means that this is likely to make it on to the factory floor quite quickly.
Science, 2019, DOI: 10.1126/science.aaw6699 (About DOIs)
https://arstechnica.com/?p=1560413