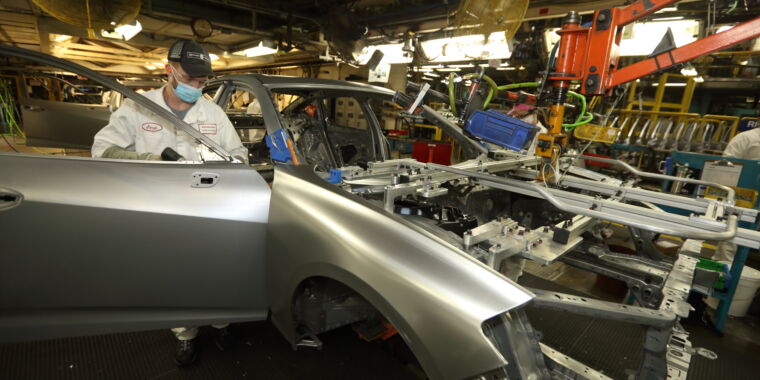
-
The new Acura TLX has just gone into production in Marysville, Ohio. It’s a much faster car to build than the outgoing model, with a stiffer chassis and sharper panel creases.
-
The TLX is the first Acura model to feature a Laser Brazed roof.
-
Acura sent a pair of TLXes to contest the exhibition class at this year’s Pikes Peak International Hill Climb. Jordan Guitar came 5th in class with a time of 11:37.219, and rookie Justin Lumbard was in 6th place with a time of 12:10.008.
-
This photo makes it easy to see the sharper creases along the hood.
Every industry has its own yardsticks—ways that competitors can measure up against each other to see who’s best. In the automotive-manufacturing world, a great way to do that is to let your body panels do the talking. Precise panel gaps are one way to do that, for example. And now that everyone has pretty much mastered the art of curves, the trend du jour is for adding sharp creases and folds. The latest Acura TLX sedan, which just went into production in Marysville, Ohio, is a good example of that.
“Our hood has a new technology called sharp edge,” explained Ken Sheridan, associate chief engineer at Honda of America’s Marysville factory (Honda is Acura’s parent company). “The radius on those styling lines—usually they’re like a five millimeter radius. In this case, they’re really sharp. They’re a 2.5 millimeter radius, and they come all the way into the bumper on the top of the car. It’s a big thing because our whole concept is this precision-crafted performance.
“It’s always a challenge once you have all this accuracy and then you put these aluminum comps—we have aluminum fenders and aluminum hoods—into our oven at about 450 degrees, and then stuff starts wants to start moving,” Sheridan told me. “So we actually developed special fixturing for that to keep it at a nominal position after it’s basically soaked in our oven.”
The body-in-white is a jigsaw puzzle
For the new TLX, the company is using a new construction technique.
“The approach we took over four years ago is going after a square body approach,” he said. “So the body is completely square and perfectly dimensioned, similar to, like, a foundation on your house. Then any parts that we hang on that square, like the doors or the fenders—we have a chance of really making a final one CBU in perfect condition.”
It’s a technique that Honda first tried out with the most recent Accord (the TLX and Accord are not on a shared platform, however). Normally, when you put a new vehicle into production, you have to spend a pile of money on tooling first, which is unique to each model. Instead, Acura is using an inner frame structure, to which it attaches the parts.
“With this inner frame structure, we’re putting the parts together more in comps, and then we’re using more robots to hold the parts in position, and we don’t need all that exclusive tooling,” Sheridan said. “So it’s more flexible, and we don’t have the new model investment every time we come on, but the accuracy is a lot better, too.”
Datum holes and datum parts
“One approach that we took, we really emphasized early, is the way we datum parts,” he explained. “So, from the time we stamp a part at a supplier and then they start making those comps, the datums that they use to build that comp, or that part of the car for us, we bring it in and we start welding those big pieces together on our process—we use the same common datum holes that they used as they made the comps.” (Previously, suppliers might use different reference points to the ones Acura used later in the build process.)
In order to make that work, Acura worked to ensure the mating surfaces (where parts are joined to each other on the car) are all extremely precise.
“It’s kind of like if you have a puzzle. If you have a corner piece of a puzzle, you have a straight edge on the top and a straight edge on the side—those areas of the puzzle aren’t so important,” Sheridan told me. “But the areas that connect those critical datum surfaces that we use, mating surfaces, is really where we focus critical control points and accuracy on. So for this model we did a lot more scanning of the actual whole part surface on those critical areas. We didn’t care about so much the top or the side of the puzzle that was straight, but anywhere where it mated we hold the supplier to a higher standard.”
Lazer Brazer
Acura is also employing a new method of joining the TLX’s roof to the sides of the car called a laser braze process. Robots use a dual-headed laser to weld the roof to the sides.
“There [are] two robots, one for each side of the car, and the first one’s cleaning and prepping the area of the surface that we’re going to do,” Sheridan said. “And then the second one’s melting steel wire 1.6 millimeters in diameter and that’s basically stitching that whole line along the car.”
At just 44 seconds, the process is considerably faster than it took to put a roof on the last-generation TLX and involves much less hassle than workers having to add temporary braces and gussets.
The result is a body with far higher torsional stiffness than the outgoing TLX—a 50-percent increase overall, and up to 100-percent stiffer for bits that really matter, like the suspension-mounting areas. Which means the new TLX should be a sharper drive than the old car, something Acura demonstrated at the end of August when it sent a pair of them to Pikes Peak for the annual hill climb.
Listing image by Acura
https://arstechnica.com/?p=1703714