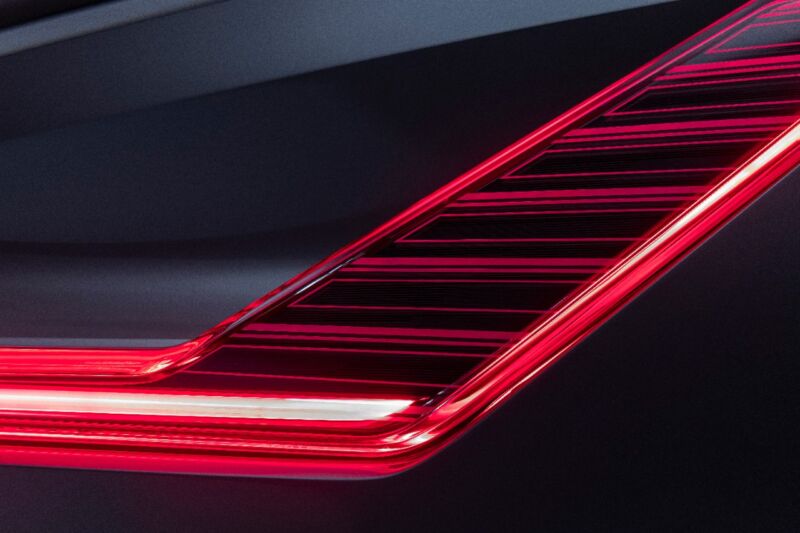
Cadillac’s transformation into an all-electric vehicle brand is about to get underway. The first new Cadillac EV will be the Lyriq, which has just entered production; Ars is driving it next week, and we’ll be able to tell you about it on June 28.
With a starting price of $59,990, the Lyriq looks reasonably priced to enter the competitive luxury EV SUV space. But the Cadillac EV that follows will be a much more exclusive machine. It’s called the Celestiq, and so far, details are scarce ahead of a formal reveal of the show car in late July. Cadillac has said that “from first approach, the striking silhouette of the Celestiq show car leaves a lasting impression, challenging the ultra-luxury space with the spirit of futurism and the avant-garde.”
On Wednesday afternoon, Cadillac revealed that it will hand-build the Celestiq and will spend $81 million to set up production at General Motors’ Global Technical Center in Warren, Michigan.
“As Cadillac’s future flagship sedan, Celestiq signifies a new, resurgent era for the brand,” said General Motors President Mark Reuss. “Each one will be hand-built by an amazing team of craftspeople on our historic Technical Center campus, and today’s investment announcement emphasizes our commitment to delivering a world-class Cadillac with nothing but the best in craftsmanship, design, engineering, and technology.”
As with the other EVs in GM’s pipeline, from next year’s sub-$30,000 Chevrolet Equinox to the four-ton Hummer EV, the Celestiq will make use of GM’s Ultium battery platform and Ultium drive motors.
But GM says it is embracing innovation across its supplier community with the hand-built EV, which will use a large number of 3D-printed components, both in polymer and metal.
For larger-volume vehicles, additive manufacturing is more useful in the prototyping stage, as the low per-unit cost of mass-producing injection-molded plastics makes that approach hard to beat. But for low-volume cars like the Celestiq, the situation is reversed, and the high cost of tooling means that 3D printing becomes a highly attractive alternative.
These components will be used cosmetically and structurally—something we saw to a small degree in the Cadillac CT4-V and CT5-V Blackwing sedans, which used 3D-printed badges on their shifters and additively manufactured components in their transmissions and HVAC ducts.
https://arstechnica.com/?p=1861241