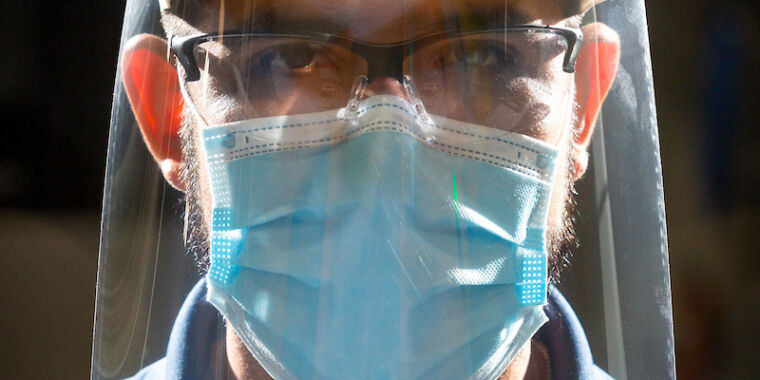
-
General Motors 3D-printed parts for more than 17,000 face shields that were donated to hospitals and first responders.
-
General Motors additive-manufacturing team members working at the still-under-construction Additive Innovation Center. The company uses a mix of printers from companies like Stratasys, Markforged, and HP.Jeffrey Sauger for General Motors
-
3D-printed ear savers help make masks more comfortable for some wearers.Jeffrey Sauger for General Motors
-
3D-printed fixtures (or nests) for ventilator production.Jeffrey Sauger for General Motors
The COVID-19 pandemic has changed the way many of us work, and that is certainly true for General Motors. The nation’s largest automaker might not be selling nearly as many cars as it hoped and has even pushed back some of its product releases (like a refreshed Bolt EV), but it’s been plenty busy. The company has switched gears and is using its resources and expertise to build ventilators and personal protective equipment like face shields to supply the healthcare sector. As it turns out, General Motors’ investment in additive manufacturing—3D printing to you and me—has played a big role in getting that effort up and running quickly.
GM is no stranger to 3D printing, having first dipped a toe into the world of additive manufacturing back in the late 1980s. These days, as the technology has matured, GM mostly uses it for rapid prototyping and testing new parts. But it has also been invaluable in making medical supplies.
“The ventilators maybe got a lot of the headlines here,” explained Kevin Quinn, GM’s director of additive design and manufacturing. But there was also Project O, “as in ‘other,’ like everything else, right? What else could we do to help support the frontline and support the healthcare workers as they were really battling this tooth and nail every day? And that was where the face shields, the ear savers, some of these other projects were born,” he told me.
“One of the big benefits is you can quickly pivot,” Quinn said. “So today, I could be printing automotive parts for development, and tomorrow, I could easily pivot and start printing something different—the face shield or the ear savers that we’ve printed here and some of the tooling for the ventilator supply—and really be able to quickly get those operations up and running, get production parts out, because we didn’t have the luxury to wait. These healthcare providers—and even our employees who were still working in some cases—needed these things for their safety, and couldn’t wait three, four, or five weeks even for a simple prototype injection mold tool to come online.”
“We were producing tooling and fixtures and jigs for our assembly plants,” explained Ron Daul, Quinn’s colleague and GM director of additive manufacturing. “We quickly pivoted—I would say overnight—to producing those same fixtures and nests for face masks at one of our plants. We were asked to produce ventilators. Same thing—all the tooling was produced for the nest, the fixtures and jigs, for a particular ventilator product.”
For the face shields, GM started with an open source design shared by a Czech 3D-printing company called Prusa Research before tweaking it a bit for production. In all, GM printed 17,000 visor pieces (the clear plastic shield wasn’t printed) to fill the gap until injection molds were ready; since then, the company has churned out more than a quarter-million face shields.
When the pandemic was ravaging Italy early in the year, 3D printing came to the rescue when a hospital in Chiari ran out of an important component for ventilators. GM also turned to 3D printing for its ventilator manufacturing, although here in a more similar manner to the way it’s employed in GM’s regular line of work. Specifically, it was on the tooling side, producing plastic nests (or fixtures) that were used in the production process.
A car is a collection of parts, and so is a ventilator
To be fair, while 3D printing helped out with this effort, getting the license-made Ventec ventilators into hospitals involved more of its other core skills.
“You might ask, ‘Why a car company?'” said Dave Wilson, VP and business and technology fellow at NI, a testing and measurement company that worked with GM and Ventec on the project. “And part of that is because they have such a tremendous supply chain. They have capability from securing materials, securing electrical components, securing petrochemical things; it’s just, astounding when you take a look at a vehicle: it’s this symphony of orchestration of a tremendous, diverse amount of things, you know, from material science, to electronics, to chemistry,” Wilson told Ars. (NI also helped in this, connecting GM with some of its own suppliers to provide necessary sensors.)
“You know a ventilator at the end of the day is a collection of parts—high-tolerance plastic parts, circuit boards, stamped parts, everything else,” Daul told me. “That’s what we do, and that’s what we woke up our supplier team to do, and they came through like they always do. We had overwhelming support to help us.”
Logistical expertise also played a big role. “We have heroic stories of planes being held, you know,” Wilson said. “Presidents of big shipping companies saying, ‘Hold that plane—we’ve got a critical shipment that has to go to Kokomo, Indiana!’ And they pulled out the stops and made it happen.”
Daul had first-hand experience of that. He told me, “When your boss calls you and tells you that it’s wheels up at the airport in 45 minutes, pack a bag, you’re going to Seattle and the mission is make ventilators, and you don’t sleep for the next three days in Seattle, and you live in a plant, trying to wake up your entire purchasing organization and get all your suppliers on board in 72 hours when there’s people’s lives at stake, it energizes you.”
That sentiment was shared by Quinn, even if he wasn’t sent halfway across the country on a moment’s notice. “It was just invigorating for our teams right now to be able to help something that was bigger than our company, something that the whole world was battling,” he said. “To know we could have even a small impact on that was very rewarding for a lot of our team for how they stepped up to that challenge.”
How’s this for a proof of concept?
Beyond the satisfaction of knowing they helped provide life-saving medical equipment, Project O and the ventilator program also helped demonstrate the worth of 3D printing to a company that is known to be extremely conservative when it comes to decision-making.
“With any new technology it’s always difficult to break through and convince people ‘OK, there’s these benefits to it,’ and they’re comfortable with how they’ve done things for a long time,” Daul said. “The reality is that using this exercise and using this opportunity to compete with speed, breaking down the barriers of decision-making and everything else, and using 3D-printing as a mechanism to break down those barriers and show a physical outcome in hours versus waiting for that injection mold or waiting for that stamping die—those are important things.”
Listing image by Jeffrey Sauger for General Motors
https://arstechnica.com/?p=1684699