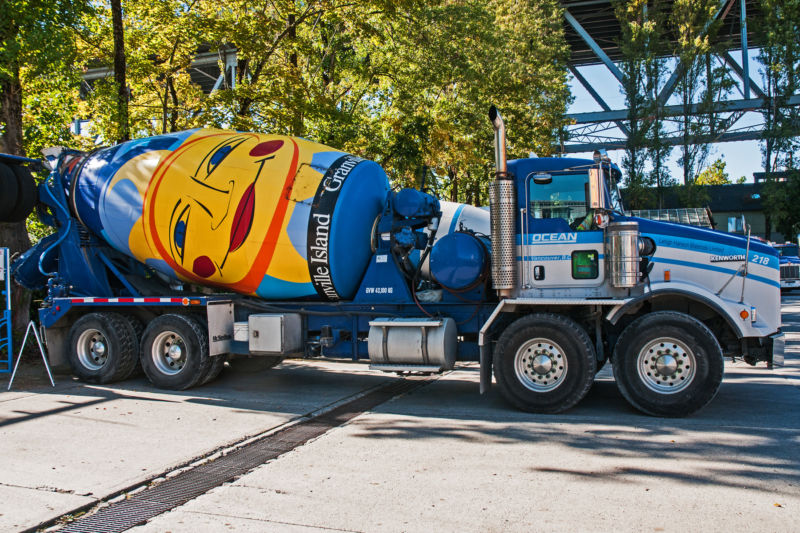
Action on climate change has been focused on the electrical grid and our transportation systems, but there are other hurdles between here and a zero-greenhouse-gas-emissions world. Agriculture and deforestation are major hurdles, but so is cement.
Producing this humble, gray, ubiquitous building material actually accounts for about 8% of global CO2 emissions. Firing the kilns required for this process is very energy intensive, but the process itself also releases CO2 from its starting materials. The primary ingredient in concrete is calcium oxide, which is taken from limestone (CaCO3)—and that leaves CO2 as a byproduct.
That means there are two problems to solve: the cement-making process needs to run on clean energy, and the CO2 that is released must be captured somehow. A new study led by MIT’s Leah Ellis outlines an option that could make progress on both.
Cement and carbon
Instead of burning fuel to heat a calciner to about 900°C (needed to liberate calcium oxide from CaCO3), they used electricity to split water. Electrolysis takes water and produces pure hydrogen and oxygen gases, but if you throw some CaCO3 in the mix, that turns into calcium hydroxide at the same time. While that’s not quite calcium oxide, it’s easy to convert the two.
The dominant type of cement out there is called Portland cement, which is formed by combining calcium oxide with silica in a kiln at an even higher temperature. The researchers performed this with the calcium hydroxide they had made and found that it worked just the same.
Of course, this was done in laboratory flasks rather than at industrial scale, but the team found that their water-splitting process worked efficiently and with pure results. But the process still needs an energy source for that kiln-heating step—and there’s still CO2 released by the reaction.
Remember this process starts with splitting water, which produces hydrogen gas and oxygen, both of which could be used to power the kiln-heating step. Pure oxygen can be added when burning fossil fuels for more efficient combustion, which would also eliminate nitrogen oxide byproducts (which are also greenhouse gases). Or the hydrogen and oxygen could be burned instead, replacing the fossil fuels entirely. Fortuitously, the amount of hydrogen and oxygen produced during the water-splitting step is roughly the right amount to fuel the kiln heating.
Easy to capture
Because the CO2 directly produced in this process is much more concentrated than normal—mixed only with the oxygen gas—capturing that CO2 would be easier and cheaper than at a conventional cement plant. And if the hydrogen and oxygen are used, the CO2 will end up purified further. What’s more, the water used at the start could theoretically all be recaptured at the end, as combusting hydrogen with oxygen produces water again, and the kiln-heating process would release the rest.
The researchers can’t estimate the real-world cost of setting up and running a cement plant of this design tomorrow, but they did run the numbers on the energy use. The water-splitting process does require about 30% more energy than a conventional coal-burning heat process, which means you need some pretty cheap electricity. It becomes cost-competitive with current coal at prices a little under 2¢ per kilowatt-hour, a price that wind turbines in the interior of the US reach today.
That’s if you’re not trying to capture your CO2, though. Doing carbon capture should cost less than half as much for this process as it would for a coal burning plant, allowing the overall costs to beat a coal plant with carbon capture by a comfortable margin.
The researchers describe this lab experiment as a proof of concept, and it would take a lot of work to engineer an actual plant that could do all this at scale. But even so, it shows that emissions-free cement is far from an unsolvable challenge.
PNAS, 2019. DOI: 10.1073/pnas.1821673116 (About DOIs).
https://arstechnica.com/?p=1569263