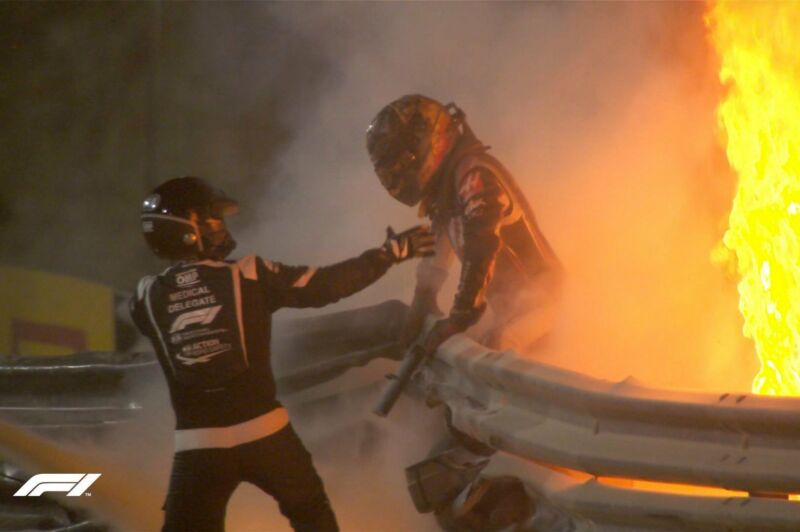
When Romain Grosjean’s F1 season came to a spectacular end in Bahrain a few weeks ago, it was the fire that really drove the headlines. High-G crashes aren’t necessarily common in the sport, but they happen once or twice a year and, thanks to rigorous design and testing, are highly survivable. An F1 car bursting into flames is a much rarer event—Grosjean’s fiery crash is the first for over 30 years, and the sight of flames strikes a kind of primal fear, bringing to mind drivers like Roger Williamson and Niki Lauda.
Just about everyone who straps into a racing car—regardless of discipline or series—does so wearing layers of a synthetic fabric called Nomex. It was designed in the late 1950s for DuPont by scientist Wilfred Sweeney, and DuPont has manufactured Nomex commercially for a little over half a century. The material’s introduction to the world of motorsport began in 1966, when racing driver and safety advocate Bill Simpson met astronaut Pete Conrad, who introduced him to Nomex. The following year, Simpson’s company supplied Nomex overalls to all but three drivers in that year’s Indianapolis 500.
Fire protection for drivers has come a long way in 53 years, and I got in touch with Yves Bader, development manager of mechanical protection and consumer apparel at DuPont, as well as Joe Foster, industry vertical manager automotive at the company, to find out how today’s fireproof fabrics have evolved since those early days.
“The polymer—a meta-aramid long chain with a high molecular weight—is the same polymer that people used then,” Bader told me. It’s related to Kevlar, but with less rigid chains than the stuff they use to stop bullets. The thing that has evolved is how to turn those molecules into fibers that you can use to make garments.
“The first generation was short spun yarn. So it was a spun yarn a bit like cotton. Then we went to filament yarn. It had this shiny look,” Bader said. “That’s when we made this fiber more dyeable because then suddenly the racing market was all about corporate images and colors and so on, which was not so important at the beginning. So you imagine the aesthetics were becoming the main point because the performance was already there, right? Then we moved to long staple fibers to get more comfort and more protection, and those fibers evolved also in dyeability, in the fineness of individual fiber—the finer the fiber, the more protection you get,” Bader told me.
Being able to make racing suits in bright colors to satisfy a team’s sponsor is obviously important—someone has to pay the bills, after all. But there’s more to it than that.
“It’s a constant challenge for us to adapt to the rule sets for the different sanctioning bodies as well. In other words, it’s a constant balance. Our performance is in weight and breathability and all of these things that make a participant want to wear it—that’s A. B—there are standards, whether it’s the FIA [which governs F1], the SFI [the US motorsports safety body], or whoever, and then you want to meet the standards, so there’s these conflicting goals sometimes. And also, the standards themselves are very different,” explained Foster.
“In the drag racing world, you’re dealing with different flammables—it’s alcohol and nitromethane and other things like that—and then so the fumes there. That’s why you see those guys wearing fume masks. And again, if you look at the gloves, for example, or the jackets or the pants that they wear in drag racing, they are like quilts, and they don’t need the dexterity, obviously. And they blow up on a regular basis, unfortunately, but those suits are quite functional,” Foster told me.
“Even though Nomex apparel for racing is not a huge market, it’s definitely a crucible developmentally, but also it’s a crucible that’s at a very high rate of speed in other words, a clock speed that most industry does not work at,” Foster said.
Some of the fabric’s protection is down to the material’s flame resistance—it just doesn’t like burning. Mostly it’s a function of Nomex’s very poor heat transmission, and drivers like Grosjean wear multiple garments to give them more time to escape the flames.
“The difficulties are always with this limited flame spread. You expose the garment to the flame and make sure that there is no hole, is no afterflame. Even the dyeing and finishing are very important—you cannot afford to have a chemical left there that could create flammability,” Bader said. Even laundering is taken into account—the FIA requires a garment has been washed 15 times before it’s tested, to ensure that cleaning it doesn’t degrade its protection.
“And then the second thing is the assembly [of the garment]. Then we apply a flame and we measure the heat transmission,” Bader said. For example, the new FIA rules require a three-layer suit to provide at least 12 seconds of protection from a flame with an energy of 80kW per square meter. “You have these 12 seconds; we design for 14,” Bader said. “Your underwear has eight seconds—it must be more than five—but the result is not 12 plus five. If you add a layer, five plus 12 becomes 20 or 22 [seconds], because you have air gaps between the layers,” Bader told me.
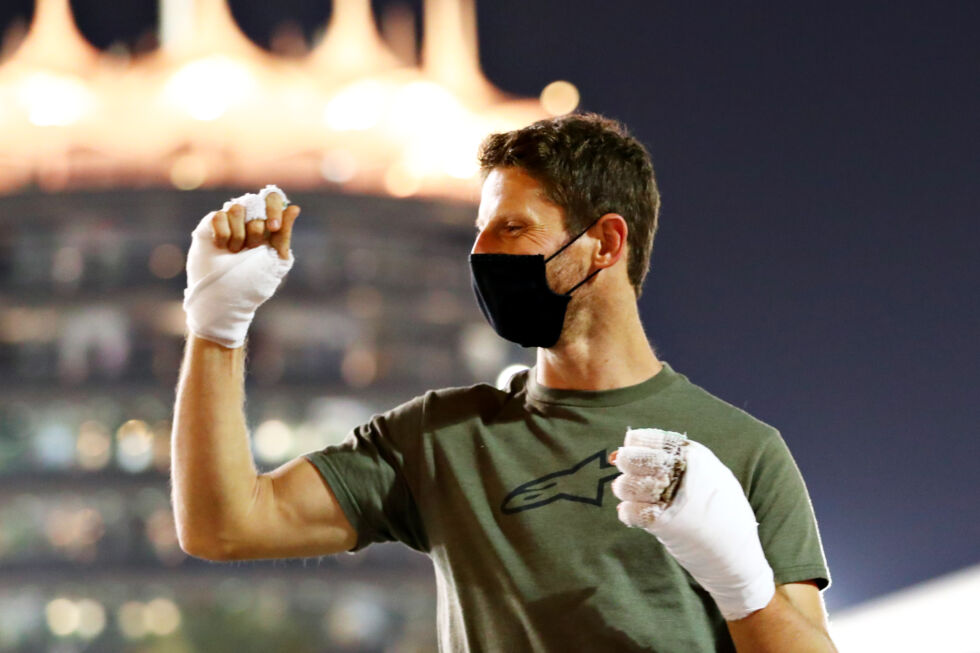
To satisfy the SFI, racing gear also has to protect against radiant heat in addition to direct flames. “Because sometimes you have flames, but the environment is already hot, and all this radiant heat is coming in addition,” Bader said.
Future Nomex fabrics should be more comfortable to wear, with better breathability, but DuPont’s main focus is on reducing weight.
“For example, Nomex fabric in workwear might have a density of 260 grams per square meter. A military pilot’s suit is 150gsm; in racing we are at 120gsm. More comfort for the driver, but it’s weight that [designers] can use in the car in an intelligent manner. And then I’m working on the next-generation glove,” Bader told me.
Currently, the standards for gloves require less protection time, and it’s notable that Grosjean’s only injuries after his crash were some burns to his hands. The issue for a racing application is ensuring sufficient dexterity, apparently. “If this next-gen glove works, that would be a game changer,” Bader said.
https://arstechnica.com/?p=1730708