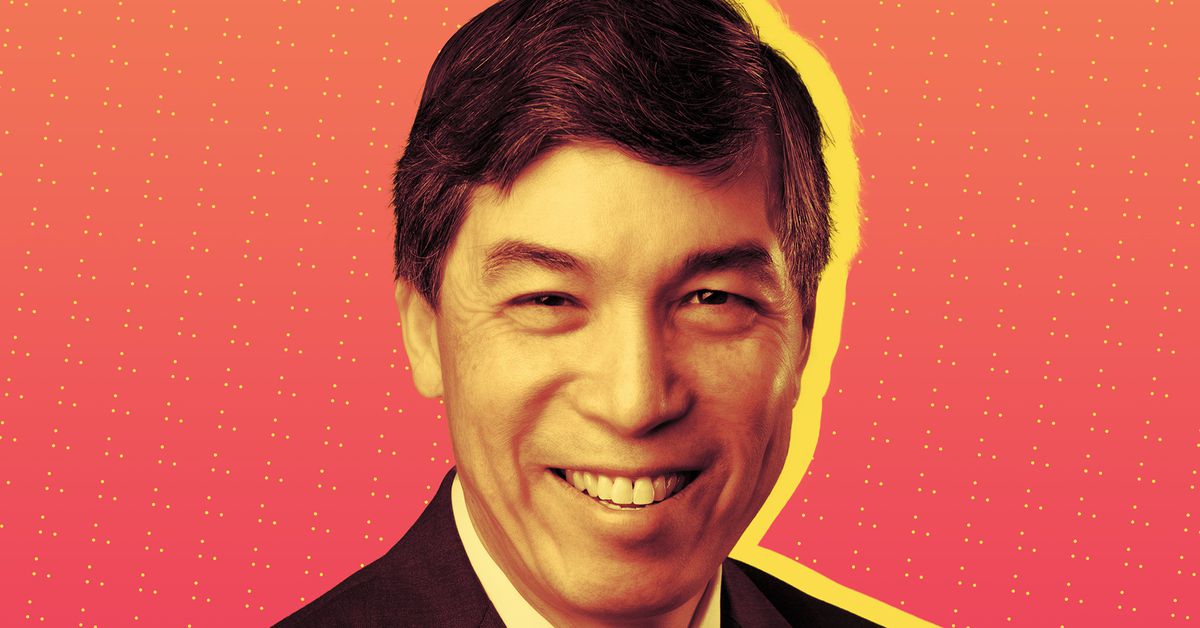
Since the beginning of the pandemic, the demand for microchips has far exceeded supply, causing problems in every industry that relies on computers. And if you’re a Decoder listener, you know that that is every industry. Right now, major automakers have unfinished cars sitting in parking lots waiting for chips to be installed. Game consoles like the PS5 and Xbox Series X are impossible to find. And even things like microwaves and refrigerators are impacted, because they contain simple controller chips.
So we realized it was time to figure out what caused the chip shortage, why that happened, and how we are going to get out of it.
My guest today is Dr. Willy Shih. He’s the professor of management practices at Harvard Business School. He’s an expert on chips and semiconductors — he spent years working at companies like IBM and Silicon Graphics. And he’s also an expert in supply chains — how things go from raw materials to finished products in stores. Willy’s the guy that grocery stores and paper companies called in March 2020 when there was a run on toilet paper. If anyone’s going to explain this thing, it’s going to be Willy.
This transcript has been lightly edited for clarity.
Dr. Willy Shih, you are a professor of management practice at Harvard Business School. Welcome to Decoder.
Thanks for having me.
You and I could talk about many parts of the supply chain that have been affected by the pandemic; before the show, we were talking about toilet paper shortages, but I want to talk about something that is a little more near and dear to The Verge; the ongoing chip shortage, which does not appear to be ending anytime soon, and indeed, doesn’t seem like anyone can forecast when it will end. So, just take a step back for everyone. Describe what the chip shortage is and what’s going on.
When we talk about chips, there’s actually a huge range of different chips. Everything from the microprocessor chips that go into your notebook computer, to the chips that go into your phone or chips that go into your Sony PlayStation console, or your TV set, or your car, or your refrigerator, or what have you. Now people tend to think, well, in my phone, I have a phone chip or two. Well, actually there are dozens and dozens of chips within a phone. In a modern car, you might have 100-plus different chips for controlling a lot of things, like the engine or all the things on the dashboard, the console, the navigation system and stuff like that. Even things like the power windows will have microprocessor chips — they’re these little controller chips because it’s cheaper to do them with chips than it is to do with mechanical linkages and stuff like that. So chips are all over the place.
And then when you see a complex product, like a car, where you can consume 100-plus controller chips and all kinds of other chips in that vehicle, what you are now faced with is, I only need to be short one of those chips, and then I can’t make the vehicle. And that’s really the problem. It’s not a problem that the bulk of the chips are short. It’s just some of them. And the “some” varies depending on the time of day, the week, the month and whatever, and what other people are buying. So it’s that problem, where we’re having these shortages that are preventing manufacturers from building the product. If you are a product manufacturer, you often talk about, is this product clear to build? Do I have all the components I need to build it? And that’s where we’re seeing the troubles now, because one chip is short or several chips are short.
There was a story the other day about Ford building its trucks minus some chips, putting them in a parking lot and just waiting, and then reinstalling the chips, because they might as well just run the plants.
Because an auto plant is a very expensive asset. You’ve got hundreds of millions of dollars tied up in that. And what you want to do is keep it running. If you’re an automaker, like one of the Big Three in Detroit, and you don’t have parts, those lines are usually producing about one vehicle per minute. So I think the average selling price for a vehicle now is over $40,000 recently. Okay, so that means every minute they’re losing $40,000 in sales. That’s a lot. So what they do is, they’ll take those vehicles out, park them in a field somewhere and hope when the chips come in, they can quickly go put them back in, but still, when you do that, then you have to bring them back into the factory and sometimes you’re going to have to disassemble something to go put the chip in. Sometimes it can be buried way in the engine compartment or way behind the dash. So, that’s a lot of additional work.
Let’s start even farther back. We talk about chips and it makes them feel like a commodity. There are obviously lots and lots of different kinds of chips and lots and lots of different process nodes from different fabs and vendors, but just at a basic level, how are chips made, where do they come from, and what is the supply chain to get to a chip?
Because when we talk about a car, it’s not like they’re just throwing microcontrollers inside the engine bay, right? They have to assemble them onto computing products, onto boards, and put those in the cars. But how do we get to a chip first?
There are really two parts. There’s the design part. And the design part involves engineers laying out a circuit, which will have transistors and it’ll have lots of other components connected in a particular way. And the way they’ll do it, these days, they’ll work on computers and they’ll design the chip using computer software, which will give you a file, which they can send to the manufacturer.
Now that design can go from relatively simple designs, which these days are hundreds or thousands of transistors, to the most complex ones, which will have 2 billion transistors in a single chip design. So when you get to those more complex design aspects, there is also a supply chain associated with that. Because if you’re going to design a chip with 2 billion transistors, the likelihood of you getting every one of those connected in the right place the first time is frankly zero. So what people do these days in modern chip design is, they use predesigned blocks called intellectual property blocks or IP blocks, which are known to work. So you decide, “I want to build a controller chip.” So you buy a processing unit design from somebody like Arm in the UK, who is very popular, and then maybe you need the USB interface, so you get a USB IP block, which you license. And the software tool suppliers have all these libraries that allow you to kind of stitch together your chip with known good blocks of logic, and then you design the stuff that you need to customize. And then you send it off to the foundry or the factory that’s going to make this chip. So that’s actually a very complex supply chain as well. You have a tool manufacturer, you have IP blocks and stuff like that. Okay, so that’s the design part.
The actual manufacturing starts with a silicon wafer. And here, what you have is somebody who makes a single crystal silicon in a giant ingot, and then they slice it into — the most advanced are 300-millimeter diameter, or about 12-inch diameter — wafers, and when they slice it and polish those wafers, they are a perfect crystal. And then what they’ll do is they will pattern the transistors and the interconnections on that wafer. Now that supply chain is fairly complex as well. You have somebody who makes the silicon ingots and then slices it into the wafers. And then those wafers go to these giant fabs (factories that manufacture the chips).
Inside the fab, the manufacturer will lay out a pattern, first, of the transistors on the silicon. And what they’ll do is multiple steps of lithography, and etching, and deposition. They’ll use a whole complex series of steps to build up layer after layer of transistors. They’ll use multiple layers to build it up. And then they’ll lay down an interconnect network of little copper wires, which they also print on there to connect all those transistors. Now in the older technologies, that’s frequently 350 steps, which might take you 45 to 60 days to go from start to finish. And some of the newer technologies, like the most advanced chips that go into your new desktop computers or notebook computers, or your iPhones and so on, those will use as many as 700-plus steps.
Now, when you think about a process that has 700 steps, you need to execute each step with very high yield. Because if you had 99 percent yield for the first step and 99 percent for the second step, you and I would think, “Wow, that’s pretty good, right?” But if you take 99 percent yield through 700 steps, by the time you’re done, you’ll get nothing at the end which is workable. So you really need to have 99.99-plus percent yield on every step. Because it’s really a drag when you get to the 690th step and then you have a low-yield step and you have to throw out all the stuff that came before. So it’s a very exacting process that takes many steps, and that’s going to take 60 days or more, to have the wafer go all the way through.
So, that’s the work that is done by the fab. Now you have a wafer that, if it is a microprocessor, might have like 500 chips on them. If it’s something like a controller for a car, you might have 4,000 chips on them because they don’t take as much space. So then what they do is they take that wafer, ship it to usually southeast Asia or China. And there are companies called outsource assembly and test factories, who will put these little probes on each chip and test which ones are good to make sure they’re good. And then the ones that are good they’ll record in the computer and they’ll remember, then they’ll cut them apart and they’ll put them into packages. So, that’s another group of companies that do that. A lot of them are in Malaysia and Vietnam. I just heard this morning that Vietnam is going to a hard lockdown on COVID. So, that’s going to affect a lot of the packaging factories there.
And after those chips are packaged, then they get sent to somebody else who will put them on circuit boards and sometimes assemble it all the way into the finished product. Sometimes it’ll go to somebody who puts them on the circuit boards, who then sends the boards to somebody else. So you have multiple tiers in the supply chain, all the way from the raw silicon, through the design, through the fab, through the assembly and test and packaging to the boards and so on. It’s a long, sequential process that crosses many national borders. And that gives you lots of opportunity for things to go wrong when you have something like COVID come in.
I don’t think I’d ever pictured a silicon ingot before, but that’s just a giant chunk of silicon that gets sliced? Like literally, a giant rock goes into one side of a factory and slices of silicon that get turned into chips come out the other side?
Well, what they do is, they melt it. So they have this giant vat of molten silicon, and then they take a crystal on this rod and they pull out something that looks like a torpedo. But it’ll be a giant ingot, which will be about a foot in diameter, 300 millimeters in diameter. There are a lot of these high-tech manufacturing processes that just boggle the mind, that people never see, but that’s what they do for silicon ingots.
If you want to see something really crazy, it’s like the flat-panel display you and I are looking at each other on right now. Those are made with sheets of glass that are a half-millimeter thick, the size of a king-size bed typically. And those are cast in a single, optically perfect sheet. Corning has a process for this molten glass that comes on two sides of a trough, overflows the trough, fuses below the trough, and then just cools as a optically perfect sheet that’s a half-millimeter thick, the width of a king-size bed, and then a robot grabs it while it’s cooling and cuts it off with a diamond cutter. So that’s even crazier. But there are these crazy manufacturing processes.
In the silicon manufacturing process, for the most advanced tool inside a fab, typically you’ll have hundreds of different tools. Actually in a large fab, like one you might see at TSMC (Taiwan Semiconductor Manufacturing Company), you’ll have thousands of these tools. And these tools are big machines that process these wafers and do various things. And most tools cost, starting with a couple of million dollars, to the most expensive tools are in excess of 150 million euros. So, well over $150 million for a single machine. And that’s for the lithography machine that actually prints the patterns on the wafer, and the lithography machines, the most advanced ones, for like if you’re looking at the chips in your iPhone, which uses TSMC’s most advanced processes, those have what’s called an extreme ultraviolet light lithography system.
And to get that extreme ultraviolet light, what they do is, they vaporize tin, the metal, with a laser. And then when the vaporized tin is dropping, they hit the drops with another laser and it generates this plasma, which emits this extreme ultraviolet. It’s crazy. And then it goes through this mirror system because you can’t use lenses with extreme ultraviolet light. You have to use mirrors to focus that down into these little narrow patterns. I’ve actually been in the factory where they make those mirrors, and the surface of the mirror is smooth to the level of one atom. So as I’m looking at these mirrors, the guys who were making them said, “Yeah, you know, if we pointed this system at the moon, right, when that beam of light got to the moon, it’d be like, I forget the exact number, 20 centimeters wide or something like that.”
What you’re describing is an extraordinarily complicated system with a lot of extraordinarily complicated technology embedded into it. I talk to a lot of consumer product CEOs on the show. I talk to a lot of software people. We tend to forget that there’s these enormously complicated manufacturing techniques in the background, enabling all of the internet, all of the digital world, to exist. And then it kind of gets flattened to the chip shortage.
When we talk about the chip shortage, we talk about COVID hitting. Is it just that the factories stop producing and making the decision to ramp them back up again took a long time? Is it consumer demand for PS5s skyrocketed? What was the inciting event of the chip shortage?
Well, when COVID hit a couple of things happened. Let’s start with the auto industry, because I think that has gotten a lot of attention because the chip shortage there has cut into production. So let’s look at the auto industry first, because I think it tells you a broader story.
When we think about the auto industry, we should remember that China is the world’s largest auto market. China typically produces and sells around 25 million vehicles a year, whereas the US production is typically around 11.5 million vehicles, and the US imports a lot of vehicles. So the China market is much larger than the US. I’m telling you this because in January 2020, the Chinese auto market was coming off two years of declining sales. So sales had dropped 8 percent in 2018. And 2019 was not so great. The China Association of Auto Manufacturers, going into January 2020, was predicting a 2 percent drop in vehicle sales, and that was before the pandemic hit.
Then the pandemic hits and vehicle sales drop 82 percent in February and 46 percent in March. Now we had a delayed reaction in Europe and in the US. In Europe, vehicle sales fell 46 percent in March and 80 percent in April of 2020. In the US, they fell 39 percent in March and 52 percent in April. Now, we have to think back to those times and remember what the news reports were. The automakers, especially the Big Three in Detroit, thought, “We don’t want to go bankrupt.” Vehicle sales are down, they’re trying to conserve cash. So they’re laying off workers, shuttering plants. It’s like, “Hey, purchasing, stop all that incoming material.” Because they’re trying to conserve cash. They don’t want to go bankrupt. Not illogical.
But at the same time, with working from home, we saw this huge spike in consumption: notebook computers, gaming systems, flat-panel TVs, exercise equipment, home appliances. I tried to buy a freezer back then and my dealer said, “Who are you kidding? Haven’t you been paying attention?” It’s like, “I haven’t been able to keep a freezer in stock for months.” And that’s because those use chips as well. So what happened is the automakers canceled orders or didn’t order, because they said, “We’re not going to need all these chips.” If you go back to May 2020, Boston Consulting Group put out this forecast that overall, 2020 global vehicle sales would drop 14 to 22 percent, in their most likely case. Their most optimistic forecast was a 12 percent drop.
Then what happens is we see this boom starting in the summer as the world starts to open up, especially the US. And by the time the auto manufacturers realized, “Oh, wow. We need to order more chips.” All that capacity, or a lot of that capacity for those chips, was already taken up by other players. … So that’s one dynamic.
Another dynamic that was going on at the time; the US had sanctioned a number of Chinese companies like Huawei. So Chinese companies, in the summer of 2020, put massive orders on these factories because they wanted to stockpile chips, not knowing when they were going to get cut off.
Chinese companies were very dependent on US chips at the time. So they started stockpiling massive numbers of chips, because that’s what allowed them to stay in business.
So the sanctions are coming six months from now, they’ll be in effect, you can’t buy Intel chips.
Well, there was a fear of that. So they were buying a lot of other chips.
Okay. So they’re just trying to get ahead of the deadline.
The threat of a deadline, or any threat of sanctions. So they were very worried about that because you shut them down, you shut down the supply and they can’t build any products.
So there was this boom in demand from China, there was a boom in demand from other companies making other products.
And then the third thing that happened was we had a number of real disruptions. Back in October 2020, there’s a Japanese semiconductor company called Asahi Kasei Microsystems, AKM. They had a factory fire. Now they were a specialist chip maker that made analog and digital converters and stuff like that, which are used in many, many products. So we had a fire there. We had the cold weather shutdown in Texas, which shut down the NXP factories in Austin and the Samsung factory in Austin. And when you take away the electricity and shut down a fab like that — they consume a lot of power, it’s not like you can keep them going on generators — to restart takes a couple of months. So then we had that. And then in March of this year, Renesas in Japan had a fire in their fab, which makes 40 percent of the microcontrollers for automobiles. So on top of all these supply-demand shifts, you actually took out a lot of capacity in a couple of small players. But again, if you don’t have those particular chips, then you’re in trouble.
How often do fires happen? I feel like because of the chip shortage, we heard about every disruption to the supply chain constantly. “There’s a chip shortage, oh no, this thing happened, it got worse.” But in a normal year, how many disruptions like that happen?
It’s relatively unusual. Now the Renesas fab was the same one that suffered a massive disruption during the 2011 Tohoku, East Japan, earthquake and tsunami. I actually visited that fab a couple months after that disruption. Because when that one went down back in 2011, it took down Toyota and Nissan and Honda, a couple of General Motors lines, I think a PSA line in Europe. And they marshaled tens of thousands of people to get that fab back online. But then companies like Toyota said, “Oh, we’re going to learn a lesson from this.” And they had much more inventory of chips. So Toyota, until recently, hasn’t suffered the same fate as some of the American manufacturers have. But generally speaking, those types of incidents are relatively rare.
One of the things that I think about a lot in terms of consumer tech coverage is that we are somewhat spoiled in that every year, Apple puts out a new iPhone with a new chip. And maybe it’s just a different name, but it’s a new chip. And often there’s a new process node, they get smaller. Every year, until maybe the past five years, there’s been new laptops with new Intel chips and then Intel kind of hit its pause. But we are constantly seeing new chips.
And I think there’s a belief in the consumer tech world that every new product has new chip technology in it. And what I’m getting from this conversation is there’s a lot of chips that have just been static, that are just commodities. General Motors is not searching for the next great process node for power window controllers. They’ve settled on what they’ve got from their supplier and they’re going for it.
How do you think about that market? How much of the chip market is, “Here’s a bunch of stuff that’s good enough, that’s worked, that’s proven. We’re just going to make it, and what we don’t have is inventory,” and how much is, “Here’s the new stuff”?
Well, I think you highlighted a very important point: there are really two different worlds. There is the leading edge, as you described. And that is mostly chips that go into smartphones, computers, data-center stuff, and high-performance chips. A large part of the world uses older process technologies. Sometimes they’re five or six generations older than what you find in your Apple iPhone. And so those chips are much cheaper to make because the technology is less demanding and the equipment is already fully depreciated. It’s already paid for. So those are much more commodity chips.
Now, even in your iPhone, you will have commodity chips like a power management chip or a display driver chip. In an iPhone it will be a little bit different, but your TV set will use display driver chips. Or there’s a category of chips which have been around for as long as integrated circuits have been around, called timer counter chips. I tried to buy some for a design exercise we do at the Harvard Business School this past year. I buy them every year. I never had trouble getting them until this year. So a lot of those old chips are older technology and they are commodities. They’re cheap. Sometimes they’re as little as 50 cents for a chip, or a dollar. And they’re a commodity and they’re not very profitable.
But it also highlights a couple of issues. As you say, a lot of people don’t distinguish between those two kinds of chips. I wrote a piece about a meeting at the White House where the president had bleeding-edge chip consumers, and chip fabs and automakers all together at a meeting. And it’s like, “Wait a minute, guys. You have two very different markets represented in this meeting. Do you understand what you’re talking about here?” And I’m not sure that they did.
The other thing that is going on in the supply chains is a lot of double ordering or hoarding, or “I’m going to just build a little more safety stock inventory.” Now, nobody wants to admit that they’re doing that because it’s kind of antisocial to do that right now. But let’s think about this problem. Let’s say you’re making notebook computers and you have plenty of chips and your competitor doesn’t. So what that means is you’re going to gain market share on them. So if you’re a competitor, they’re saying, “Yeah, there’s no way I’m going to lose market share to those clowns. Order extra chips.” And so everybody’s very conscious of, “If I have chips, I gain market share. If I don’t have chips, I lose market share. I’m going to make sure I have extra chips.” So when you have people who are ordering extra in a supply crunch, what happens? It makes it worse.
Do you think the split between the PS5 or the Xbox Series X, which people are struggling to purchase, and the carmakers unable to get chips to complete their cars are related to the same root problems? Or are they different causalities?
You would have to look at the individual product build materials and the specifics. So I can’t speak with authority on the specifics, but what I do observe is you have this tiering in the supply chain. So for example, if I’m an automaker, what I’ll do is historically I would buy key subsystems from my tier-one suppliers, Bosch or Continental or somebody like that, who might buy a circuit board from somebody else who will then use a chip that was made by, say, NXP, or maybe Infinian or Texas Instruments, who may have made the chip themselves. Or they may have gone to somebody like TSMC to make the chip.
Now what happens is you have a group of companies that are called “fab light.” In other words, they have some of their own manufacturing, but the more advanced manufacturing they outsource to the foundries. And I think what happened is people didn’t realize that when I get all the way down through that stack, I may share a foundry with somebody in another industry that I didn’t realize. Okay. So then it becomes a question, if you’re TSMC or one of the other foundries, “How do I allocate my capacity?” And I don’t know if this is what’s happening, but I do know that the US administration, the Germans, a lot of other countries, got on the phone to TSMC and said, “You have to allocate more capacity to our auto industry, because I have all these people who are out of work because we can’t assemble cars.” And TSMC did ramp up the number of chips that they’re sending to the auto industry. Okay, so then the question is, who else got shorted?
One of the things that I have seen play out, we talk to a lot of car company CEOs on Decoder. The CEO of Ford was on the show. He said, “Look, I used to just place orders to my tier-one suppliers. Now Ford is in the business of buying chips directly because I don’t want to be in this situation again.” That feels like a reordering of the supply chain, when the final assembler is saying, “I’m going to start buying components directly in a way that I haven’t before.” Is that having a spillover effect into how the entire chip supply chain is working, or is that a moment in time?
We will see. I went to an event where one of the big foundries was announcing an expansion, and they had guests from the automakers who articulated exactly that: “We have to be a strategic partner with the chip manufacturers.” That’s to say, I am going to go from what has historically been a very transactional and punitive relationship with my suppliers to a strategic and a partnership relationship with my suppliers. What I will observe about that is Toyota has always had that approach, and they have fared much better in the pandemic.
But let me ask you this. You can describe it as punitive, but it’s also competitive, right? They have multiple suppliers. The suppliers compete. They can fire suppliers if they don’t do well, or they have higher prices. One of the themes of the tech industry right now is consolidation. Chip foundries are largely consolidated.
There’s only a handful of them in the world. TSMC seems to be at the center of a lot of these conversations. Is that consolidation good? Is it getting split out? Is there a sense that maybe the fate of the world shouldn’t be in the hands of three foundry companies?
Less diversification is not necessarily good from an innovation standpoint, because what you really want is innovative new ideas and innovative new designs coming to the fore. So if you consolidate them down to a couple of suppliers, I’m not sure how that is going to play out. We see that chip consolidation is certainly going on. A lot of that is driven by the capital and scale requirements to be a manufacturer these days.
If you’re an automaker, when you design a chip and you qualify it, you plan to use that chip for the whole model run. So it’s not like you can switch out in the middle, unless you design it with the idea that “I am going to be able to accommodate two different parts or three different parts, so that I could substitute them when they come in.” We saw during the shortages that Tesla redesigned some of their parts to use different chips, because they couldn’t get the chips they had been using.
Historically, the automakers haven’t done that because it costs more. What they want to do is they want to qualify one fab to make one part. Before an automaker will use the parts from, say, TSMC, the fab has to be qualified, and that chip has to be qualified, then you’re going to use it for the whole model run. So I’m not really convinced that it’s going to change that much, because in some sense, they were already locked in.
You said it takes a long time and a lot of money to build a fab. How long and how much money?
So first they have to build the building, and then you have to move all the equipment in, you have to get it clean and qualified and up and running. In Asia, they’ll build these things in a year. They’ll move in equipment in the second year, get it qualified, running, by the end of the year. In the US, or in the West, it takes a lot longer, because we don’t have the same mentality they have in Asia. We’re going to do all the permitting, all the hearings, and all that stuff. So it wouldn’t surprise me if it took 50 percent longer to twice as long.
Now, let me tell you why that’s a problem. Because to your second question, a modern fab these days, one of the closer-to-leading-edge ones will cost you $10 billion-plus for the smallest efficient scale, and a really efficient scale will probably cost you closer to $20 billion. Think about how much depreciation that can generate. In Asia, the mentality is every day, every hour this thing isn’t running costs me tens of thousands, hundreds of thousands, sometimes millions of dollars. I’ve been in Asia on Christmas Day, and there are people out there with jackhammers and pouring concrete because it was like, “Man, every minute this thing gets done sooner, we can start generating cash.” We do not have that mentality in the West.
We’re not going to culturally change that mentality, but is that something that can be overcome with policy to make it go faster? There’s a lot of emphasis on this problem.
It can help if what we do is get the permitting to go a little faster than it typically does. GlobalFoundries built that fab in Malta, New York, at relatively good speed. They had a lot of subsidies from the state of New York. I forgot exactly how long it took to get all the permits and get the construction going, but it’s slower. There is more of a sense of urgency these days, but we still don’t have that mentality. And not to be critical, the administration talks about good union construction jobs, so they cost more. And so you just have to fold that into the cost, and eventually you have to recover that in your cash flow.
Right now, the Biden plan, I think it’s $50 billion or $52 billion in incentives, subsidies. Is that enough? Is that the first payment? Is this something that needs to continue to start building more chips in the United States?
I would say it’s not bad for a down payment. I had somebody from deep within Washington call me up and ask me how much money it would take to catch up with TSMC. I had just been to the GlobalFoundries fab in Malta, New York, and they had spent $15 billion to get 30,000 wafer starts per month at 14 nanometers — so it’s not even leading edge, but it’s a nice fab. They’ve done a good job there. TSMC Fab 12 has a capacity of 250,000 wafer starts per month. TSMC Fab 14 has about 250,000. TSMC Fab 15 has about 250,000. TSMC Fab 18, they’re targeting the same capacity. So I told this person, “Oh, I don’t know. You’d probably have to spend 10 times what GlobalFoundries spent up in Malta, New York.” I could hear him fall out of his chair.
And when he got back up, he said, “What did you say?” And I said, “I don’t know, 10 times that, $150 billion. Maybe it’s not $150 billion. Maybe it’s $130 or $140 billion. But you have to realize that TSMC is going to spend over $30 billion this year, and that’s one company. And they spent $20-plus billion last year, and they’ve been spending $10 to $20 billion a year for the last decade. And they’d been spending like $5 to $10 billion a year for the decade before that. So they’ve been pouring money into this for 35 years. So $52 billion — and by the way, all the lobbyists are in there trying to make sure that their company gets their share of it. By the time it gets peanut-buttered around, the worry will be, how much difference is it actually going to make?
Let’s talk about that for a second. So TSMC obviously spends a lot of money. They are the bleeding-edge fab. They have the most sophisticated process nodes. They make the most sophisticated chips. Next to that, you do have companies like Intel in this country that are trying to pivot to offer those kinds of services to get on those process nodes to do those kinds of things. You have a GlobalFoundries. This is a business with explosive demand, customers with huge pockets. Why isn’t Intel just saying, “We’re going to do a capital raise and spend this money?” Because they will get the return.
I think Intel, under their new CEO, Pat Gelsinger, is going to spend the money. They’ve already committed $20-plus billion to two new fabs in Arizona and New Mexico. Gelsinger has been in the news visiting France and Europe, saying, “Hey, if you want to contribute in the form of a subsidy, maybe we’ll build more fabs in Europe.” Intel already has a large fab in Ireland, and they have a large and very important fab in Israel as well. So Intel does have a global footprint. I think Intel is out to try to climb back to the top of the ladder. Intel does have a lot of capabilities. I think the challenge facing all of the big guys, Intel, TSMC, as well as Samsung, is that the risk of making a wrong technology choice is really extreme these days.
And so they may not be as adventurous as they need to be, although I think Intel seems to be showing signs of being willing to take some risk right now. One could argue, for example, that Intel was the leader for so many years, but then they were conservative on extreme UV. They held back, and didn’t invest in a lot of manufacturing capacity when TSMC did. And that’s one of those examples of not taking enough risk, being more risk-averse. TSMC bet right. Intel didn’t bet right on that, and hence they’re a little behind. That doesn’t mean that they couldn’t catch up by taking some risks, by throwing a lot of investment into the basic R&D.
Let’s talk about TSMC for one second. They are the center of the universe for a lot of the consumer tech stuff we talk about. All of the most advanced products that we cover at The Verge tend to have something made by TSMC in them. What kind of company are they? When people think about the chip shortage writ large and TSMC is sitting in the middle of it, how should they consider TSMC?
They should look at TSMC as somebody who is doggedly persistent. TSMC was spun off from ITRI, the Industrial Technology Research Institute in Taiwan, in the 1980s. Pursuing this foundry model, they really created the foundry model, which is: send me your design and I will manufacture it for you. In those days that was work that most chip manufacturers didn’t want to do because it was capital-intensive and it was hard work. And throughout the ‘80s and the ‘90s and the early 2000s TSMC just doggedly worked on improving their product offerings and became a very service-oriented company. In other words, their role is to serve the needs of their customers.
A lot of people in the US looked at it and said, well, they’re willing to do this. It’s not a very profitable business and they can do it better than me. So why should I do it?
Now what actually happened in that process is they learned and they got very good at it, and they got scale, and they were able to aggregate scale across multiple customers. And in the semiconductor business, scale is very important because how you get yield, how you get process improvement is by making chips, selling them to people, and learning how to do it more efficiently. So they were able to aggregate scale across multiple different customers, something that a lot of the American fabless companies and policymakers didn’t think was going to be possible, but they did it. And they have invested doggedly. When GlobalFoundries was established, they took that as a mortal threat. And then they invested like crazy to get out ahead of them. So you have to look at them with the utmost respect for what they have done.
When you think about a company like Intel telling the American government, hey, we cannot allow every chip in the world to be made in Asia, in that region, which has instability because of China, especially the China-Taiwan relationship implies some instability. We need to spend the money to build the stuff here. And you see TSMC in Arizona, and other places. How do you think that plays out from the perspective of American foreign policy affecting consumer supply chains?
Well, I’m not a big fan of subsidies as a way of “leveling the playing field.” You hear all the lobbyists and everybody talking about how it costs less to do things in Taiwan or Asia because of subsidies and so on. There are tax abatements and other things. But I look at some of the reports that people send me on the level of subsidies in Taiwan. And then I go to my friends in Taiwan and I want to know what their electricity rate is because one of the reports I saw claimed that electricity is cheaper in Taiwan. Then I go to Taiwan and the Taiwanese tell me, actually, electricity is more expensive in Taiwan than it is in the US — of course, it depends where in the US.
So I look at this whole “how do we get more chip manufacturing in the US” — manufacturing goes with innovation. If you want to advance the process technology, you need to know the manufacturing, so to say that we’re not going to do the manufacturing means we’re going to preclude ourselves from participating in a lot of innovation. That part in my mind is, without question, very important. Now, is it important to diversify our supply chains in this new geopolitical world? I think it would be helpful, but we should not be naive about how interdependent the world is. So for example, if we make the chips in the US, are we still going to send them to Southeast Asia or China for packaging? So then how much geopolitical risk have you really taken out?
Is that conversation as sophisticated as that?
No.
When you hear about the subsidy packages, are people like, “Then we have to package them”?
No, it’s not that sophisticated. That’s one of the reasons I try to educate as many people as I can about how complex this is. So for example, the Biden administration produced that 100-day report on critical supply chains. And they sent it to me the morning it came out and I read the whole thing, which was a long report. It was 220-some pages, I read the whole thing. And my response to that was okay, after you’re done with those four supply chains, I’ll give you another four where we’re dependent on various parts of the world for all those different pieces. And when we’re done with those four, I’ll give you another four. And when you’re done with those four, I’ll give you another four. And how long would you like to play this game?
I do think it’s important for us to be able to manufacture the most advanced semiconductor technology in the US, because as I said, that’s important for innovation, but if you think you’re going to be an island, not dependent on the rest of the world for anything else, then all you’re doing is echoing Xi Jinping’s dual circulation strategy, which is “I want the world to be dependent on me, but I don’t want to be dependent on anybody else.” I don’t think it’s going to happen.
When we look at the plants being proposed in the United States, there’s the Samsung factory in Texas. There’s a couple of big fabs being proposed in Arizona. These are places that are being hit by climate change. The Samsung fab had to shut down. Arizona’s in a desert.
Chip manufacturing is very water-dependent. Is that something that plays into this whole conversation? Where we put these fabs, how much power they need, how much water they need, is actually more important than a tax subsidy package from a lesser-regulated state.
Absolutely. I had somebody call me from Arizona asking me, what can we do to get the Samsung fab located in Arizona? And I said, get more water. And they said, we have plenty of water. I said, but the Colorado River Compact is coming up for renegotiation. And you guys are in a historic drought for the last 20 years. And you need a lot of water for chip manufacturing. Taiwan is having a drought because normally their reservoirs are filled by the typhoons over there. And they had a very dry year. In Taiwan they were trucking water to the fabs. So all those resource constraints are important. And I don’t know why we like to build fabs in deserts. By the way, that was a lesson that goes back; I first heard that 25-plus years ago, because Intel has a fab in New Mexico on the Rio Grande, just on the north side of Albuquerque. And I was at a company, we had a factory just downstream from that fab. And they had come to us asking for more of our water allocation. Guys, this is a desert.
It’s just part of this where it seems like we are in the United States trying to create more supply in the future. And there’s many challenges along that road. In the meantime, you’re looking at TSMC and a handful of other companies elsewhere in the world who can meet the booming demand. The demand may or may not abate. People aren’t going to stop buying stuff — it might change. But as these new facilities come online, we’re going to add a lot of chip supply after the problem is solved. It doesn’t seem like these things are aligned at all to me.
I agree with you. Do you want to know what I would do?
What’s that?
I would invest in the basic science. And let me give you a parallel example. When we look at these mRNA vaccines for COVID-19, a lot of people look at that and say, what a spectacular accomplishment, all these US companies, Pfizer and Moderna, they did it in 18 months. Well, actually, that’s not exactly true because mRNA vaccines were first proposed in 1990. Moderna, for example, had been working on it for a decade with $1 billion of private capital invested. But what really happened was in the late ‘80s into the 1990s, the US government invested huge amounts in genomics, the human genome program, biotechnology, molecular biology, life sciences, health sciences in general. And we had this wave of innovation and discovery, which laid the foundation for companies like Moderna, technologies like mRNA vaccines. And by the way, DARPA had funded pandemic preparedness research at Moderna half a decade ago.
So when the pandemic hit, we were able to pivot and then BARDA, the Biomedical Advanced Research Development Agency, could put $10 billion into it and say “Let me speed up your manufacturing. Let me speed up your clinical trials.” And we see what the result of that was.
If we invested in that leading-edge semiconductor technology, then companies like TSMC and Samsung would say, “I have to put more factories closer to where this innovation is because that research establishment in the universities or wherever the research is being done is training people. And that’s what I need to run all these places.” I told one person in Washington, I said, if you look at the investments in genomics and biotech, back in the early 2000s, Novartis, the Swiss pharmaceutical giant, moved their R&D headquarters from Basel, Switzerland, to Cambridge, Massachusetts, to be in the heart of it. And all these other global pharma companies have done the same thing. They’ve moved to the US. They moved to the Massachusetts Bay area because they have to be close to where the leading-edge research is. That is what we should be doing.
Do you see any glimmer of that happening right now in any of the administration proposals?
Well, I see people talking about it. I try to articulate that, but the challenge is this is a very complicated picture, and you have to understand all the moving parts and you have to understand the long time horizons in some of these solutions. And it’s a challenge because a lot of people haven’t been inside these fabs, haven’t looked at this problem, don’t understand the basic technology. So as an educator, one of my goals is to try to teach people as much as I can about this stuff.
We ask a lot of CEOs, when do you think the chip shortage will be over? It’s always farther out than I want. And it’s never certain. It seems like it’s going to persist for a long time. When do you think it will be over? And do you think it will be over?
Well, it’s not going to be like the tape breaks at the finish line, and there’s a clear ending to this thing. Rather, it’s going to be that some sectors are going to get better sooner than others. I think if you’re looking for “When are we going to stop talking about it because the problem is not as severe?” I think it’s going to be the middle of next year.
And that is because supply will rise to meet demand, or because demand will taper off?
A combination of things. Supply will rise to meet demand. Demand will stabilize at a more rational level and people will have a lot of inventory to work off.
When you say demand will stabilize, is it that people have just bought enough laptops?
Well, yes. One of the things that I find really comical about this is listening to some of the product makers say that they think laptop sales are going to continue at the same rate as the last year. They’re forgetting that these things last more than a year, and they actually have an upgrade cycle which had been typically three years going on five. And you have to believe during the pandemic, a lot of those upgrades were pulled forward, so my advice to people, if you can wait, you’ll get a good deal in not too long.
Yeah. That’s great advice. Well, Professor Shih, it was amazing to talk to you. Thank you so much for being on Decoder.
Thanks for having me.
https://www.theverge.com/2021/8/31/22648372/willy-shih-chip-shortage-tsmc-samsung-ps5-decoder-interview